Special welding machine system for rapid metal forming through electric arc method and control method of special welding machine system
A metal rapid prototyping and arc method technology, applied in arc welding equipment, metal processing equipment, manufacturing tools, etc., can solve problems such as the inability to eliminate thermal stress
- Summary
- Abstract
- Description
- Claims
- Application Information
AI Technical Summary
Problems solved by technology
Method used
Image
Examples
Embodiment 1
[0057] Such as figure 1 , figure 2 As shown, the special welding machine system used in this embodiment for arc metal rapid prototyping includes a controller and a frame 01, and the controller is communicated with an external computer; it also includes an arc power supply 02, a wire feeding assembly 03, and a voltage comparison device 04; the wire feeding assembly 03 is provided with a metal wire 05, and the controlled end of the wire feeding assembly 03 is connected to the control end of the controller; the frame 01 is provided with a three-dimensional motion device 06, and the controlled end of the three-dimensional motion device 06 is connected to the The control end of the controller is connected; the three-dimensional motion device 06 is respectively equipped with a welding torch head 07 connected with the wire feeding assembly 03 and a welding bottom plate 08, and the metal wire 05 penetrates the welding torch head 07; the welding torch head 07 and the welding bottom pl...
Embodiment 2
[0070] The welding machine system control method of the present embodiment adopts the special welding machine system used for the rapid metal arc prototyping in embodiment 1; as Figure 7 As shown, the control method of this embodiment includes:
[0071] The first step is to start the welding machine system; the arc power supply 02 supplies electricity to the metal wire 05 through the welding torch head 07, and supplies electricity to the welding bottom plate 08 at the same time; the voltage comparison device 04 passes its first voltage detection terminal A and second voltage detection terminal B Monitor the real-time voltage between the wire 05 and the welding base 08;
[0072] In the second step, the external computer models the printing target, slices the model layer by layer, and obtains motion control commands and wire feeding control commands based on the sliced data and inputs them into the controller; the controller controls the 3D motion device according to the inpu...
PUM
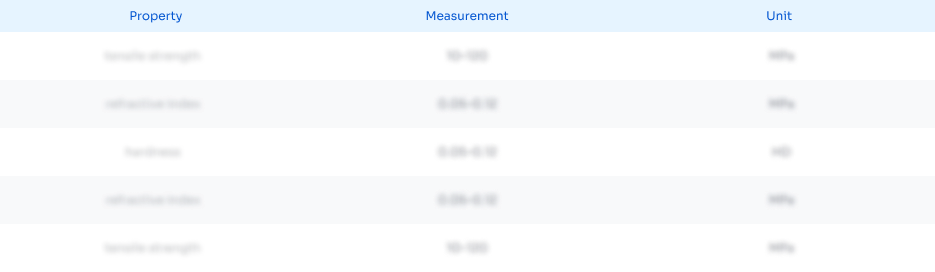
Abstract
Description
Claims
Application Information

- Generate Ideas
- Intellectual Property
- Life Sciences
- Materials
- Tech Scout
- Unparalleled Data Quality
- Higher Quality Content
- 60% Fewer Hallucinations
Browse by: Latest US Patents, China's latest patents, Technical Efficacy Thesaurus, Application Domain, Technology Topic, Popular Technical Reports.
© 2025 PatSnap. All rights reserved.Legal|Privacy policy|Modern Slavery Act Transparency Statement|Sitemap|About US| Contact US: help@patsnap.com