Process method for controlling scab defect of continuous casting slab
A process method and crystallization control technology, which is applied in continuous casting process and process field in iron and steel metallurgy, can solve the problems of continuous casting mold breakout, affecting the quality of billet, affecting the normal production of continuous casting, etc.
- Summary
- Abstract
- Description
- Claims
- Application Information
AI Technical Summary
Problems solved by technology
Method used
Image
Examples
Embodiment 1
[0024] Embodiment 1: A process for controlling the scarring defect of continuous casting slabs, the method comprises the following steps:
[0025] (1) Control the vibration precision deviation of the crystallizer;
[0026] The mold is the heart of the continuous casting machine. The precision deviation of the mold vibration refers to the degree of deviation between its displacement track and the ideal track during the movement of the mold, which directly affects the production of the continuous casting machine and the quality of the slab. Vibration deflection control includes guidance accuracy and vibration phase difference, and the control requirements are as follows:
[0027] 1) Guidance accuracy: left and right direction ≤ ± 0.15mm; front and rear direction ≤ ± 0.1mm; height direction amplitude deviation ≤ 3% (full stroke);
[0028] 2) Vibration phase difference (that is, whether the amplitude of each point reaches the maximum value at the same time): vibration phase diffe...
PUM
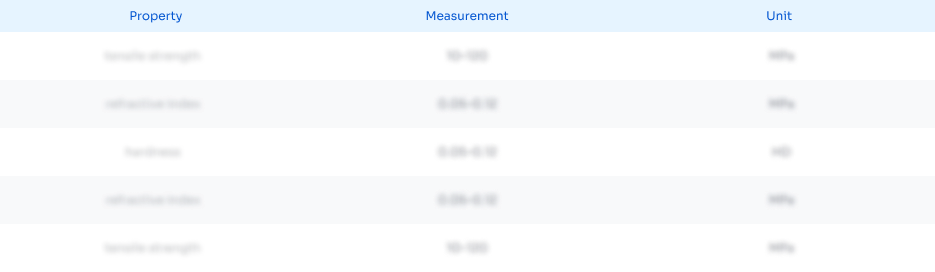
Abstract
Description
Claims
Application Information

- R&D Engineer
- R&D Manager
- IP Professional
- Industry Leading Data Capabilities
- Powerful AI technology
- Patent DNA Extraction
Browse by: Latest US Patents, China's latest patents, Technical Efficacy Thesaurus, Application Domain, Technology Topic, Popular Technical Reports.
© 2024 PatSnap. All rights reserved.Legal|Privacy policy|Modern Slavery Act Transparency Statement|Sitemap|About US| Contact US: help@patsnap.com