Workpiece main shaft and grinding machine tool
A workpiece spindle and electric spindle technology, which is applied to the parts of grinding machine tools, grinding/polishing equipment, manufacturing tools, etc., can solve the problem of difficult to achieve ultra-precision machining accuracy, poor coaxiality of inner circles at both ends, and workpiece spindle positioning Accuracy, rotation accuracy, radial stiffness and axial stiffness cannot meet the requirements of precision and ultra-precision grinding processing, etc., to meet the processing requirements of precision and ultra-precision grinding, improve processing accuracy, and improve the effect of workpiece surface quality
- Summary
- Abstract
- Description
- Claims
- Application Information
AI Technical Summary
Problems solved by technology
Method used
Image
Examples
Embodiment Construction
[0034] This part will describe the specific embodiment of the present invention in detail, and the preferred embodiment of the present invention is shown in the accompanying drawings. Each technical feature and overall technical solution of the invention, but it should not be understood as a limitation on the protection scope of the present invention.
[0035] In the present invention, if there is a description of directions (up, down, left, right, front and back), it is only for the convenience of describing the technical solution of the present invention, rather than indicating or implying that the referred technical features must have specific Orientation, construction and operation in a particular orientation, therefore should not be construed as limiting the invention.
[0036] In the present invention, "several" means one or more, "multiple" means more than two, "greater than", "less than", "exceeding", etc. are understood as excluding the original number; "above", "belo...
PUM
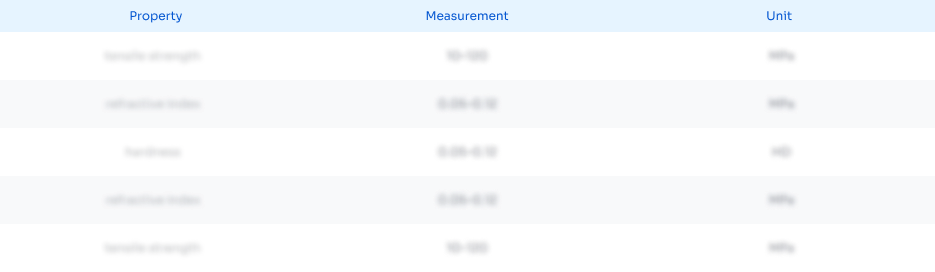
Abstract
Description
Claims
Application Information

- R&D Engineer
- R&D Manager
- IP Professional
- Industry Leading Data Capabilities
- Powerful AI technology
- Patent DNA Extraction
Browse by: Latest US Patents, China's latest patents, Technical Efficacy Thesaurus, Application Domain, Technology Topic, Popular Technical Reports.
© 2024 PatSnap. All rights reserved.Legal|Privacy policy|Modern Slavery Act Transparency Statement|Sitemap|About US| Contact US: help@patsnap.com