An automatic production line and process of an inner ball cage cage
A cage and inner ball cage technology, applied in the direction of manufacturing tools, metal processing equipment, grinding feed movement, etc., can solve the problems of scattered processing equipment, low production efficiency, upside-down placement, etc.
- Summary
- Abstract
- Description
- Claims
- Application Information
AI Technical Summary
Problems solved by technology
Method used
Image
Examples
Embodiment 1
[0062] like figure 2 , image 3 , Figure 5 and Image 6 As shown, an automatic production line of an inner ball cage cage, including a feeding system 1, a window processing system 2, an outer circle processing system 3, an inner diameter processing system 4, and a cage for detecting and not conforming to the surface to be processed an inversion system 5 for inverting and a delivery unit 6 for transporting the inverted cage to the window processing system 2;
[0063] The turning system 5 is installed above the end of the feeding system 1 through a bracket 51, which includes:
[0064] Rotary unit 52, it is installed on the support 51;
[0065] Lifting unit 53, it is installed on the end of rotating unit 52; And
[0066] The mechanical detection grabbing unit 54 is installed on the output end of the lifting unit 53 through a connecting frame 541 and includes a positioning cylinder 542 adapted to the inner shape of the holder, and several positioning cylinders 542 evenly di...
Embodiment 2
[0092] like Figure 9 It is a structural schematic diagram of Embodiment 2 of the automatic production line of an inner cage cage of the present invention; Figure 9 As shown, the components identical or corresponding to the first embodiment adopt the reference numerals corresponding to the first embodiment. For the sake of simplicity, only the differences from the first embodiment are described below. This embodiment two and Figure 2-8 The difference of the shown embodiment one is:
[0093] The window processing system 2 can match multiple outer circle processing systems 3 and inner diameter processing systems 4 according to the actual production tempo, so as to realize the matching of the machining tempo of different stations, improve production efficiency, and reduce equipment investment costs.
Embodiment 3
[0095] Referring to Embodiment 1, a fully automatic production process of an inner cage cage of the present invention is described,
[0096] like Figure 17 As shown, a fully automatic production process of the inner ball cage, including:
[0097] Step 1: Loading process, the cage blanks are loaded into the screening tray a11, and the blanks are transported to the bottom of the turning system 5 one by one by the conveying device 12;
[0098] Step 2: The positioning surface detection process, conveying to the cage directly below the turning system 5, the sensor a81 receives a signal, the conveying device 12 stops, and at the same time the lifting unit 53 stretches out, driving the mechanical detection and grasping unit 54 to move downward, when When the positioning face faces downward, the swing rod 5432 does not move at this time, and no signal is transmitted to the sensor b82. At this time, the lifting unit 53 retracts, and the feeding system 1 works to transport the cage to...
PUM
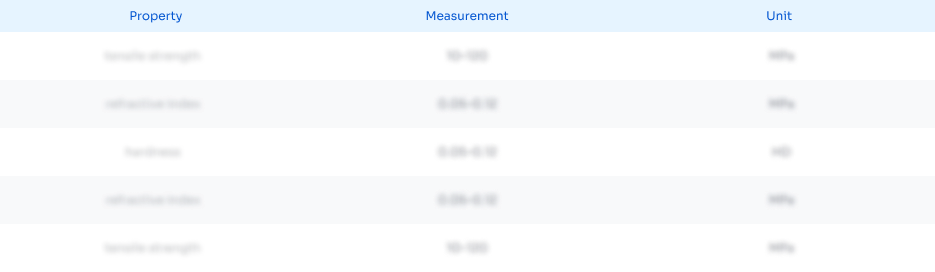
Abstract
Description
Claims
Application Information

- R&D
- Intellectual Property
- Life Sciences
- Materials
- Tech Scout
- Unparalleled Data Quality
- Higher Quality Content
- 60% Fewer Hallucinations
Browse by: Latest US Patents, China's latest patents, Technical Efficacy Thesaurus, Application Domain, Technology Topic, Popular Technical Reports.
© 2025 PatSnap. All rights reserved.Legal|Privacy policy|Modern Slavery Act Transparency Statement|Sitemap|About US| Contact US: help@patsnap.com