Rolling force detection structure of rolling mill
A technology for detecting structure and rolling force, applied in metal rolling, metal rolling, length measuring devices, etc., can solve problems such as inability to compensate contact surface wear, wear of wear-resistant plate of roll changing trolley, and aggravated wear of roll changing mechanism, etc. , to achieve the effect of avoiding layer-by-layer superposition structure, reducing contact surface, reducing workload and difficulty
- Summary
- Abstract
- Description
- Claims
- Application Information
AI Technical Summary
Problems solved by technology
Method used
Image
Examples
Embodiment Construction
[0024] Below in conjunction with specific embodiment, further illustrate the present invention. It should be understood that these examples are only used to illustrate the present invention and are not intended to limit the scope of the present invention. In addition, it should be understood that after reading the teachings of the present invention, those skilled in the art can make various changes or modifications to the present invention, and these equivalent forms also fall within the scope defined by the appended claims of the present application.
[0025] Such as Figure 4 The rolling force detection structure of a rolling mill shown includes a pressure equalizing plate 1 , a pressure sensor 2 , a compensation backing plate 3 and a roll changing trolley 4 .
[0026] The pressure equalizing plate 1, the pressure sensor 2 and the compensation backing plate 3 are stacked and fixed in sequence to form an integral pressure sensing unit. The pressure equalizing plate 1 and the...
PUM
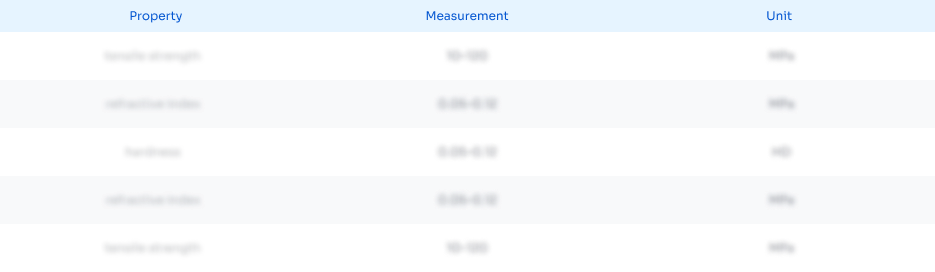
Abstract
Description
Claims
Application Information

- Generate Ideas
- Intellectual Property
- Life Sciences
- Materials
- Tech Scout
- Unparalleled Data Quality
- Higher Quality Content
- 60% Fewer Hallucinations
Browse by: Latest US Patents, China's latest patents, Technical Efficacy Thesaurus, Application Domain, Technology Topic, Popular Technical Reports.
© 2025 PatSnap. All rights reserved.Legal|Privacy policy|Modern Slavery Act Transparency Statement|Sitemap|About US| Contact US: help@patsnap.com