Dynamic and static cavity flow micro-groove drag reduction design method
A design method and micro-groove technology, applied in computer-aided design, design optimization/simulation, calculation, etc., can solve problems such as lack of curve design methods
- Summary
- Abstract
- Description
- Claims
- Application Information
AI Technical Summary
Problems solved by technology
Method used
Image
Examples
Embodiment Construction
[0036] The present invention will be further described in detail below in combination with specific embodiments.
[0037] A design method for drag reduction design of micro-grooves in dynamic and static chambers, comprising the following steps:
[0038] S1. Micro-groove space profile equation;
[0039] Fluid radial velocity:
[0040]
[0041] C r =1.18 (10 -5 · Re r +2) -0.49 (2)
[0042]
[0043]
[0044]
[0045]
[0046] v r is the fluid radial velocity, and the radial coordinate is its independent variable; C r is the radial velocity coefficient of the rotor; r is the radial coordinate; ω is the angular velocity of the rotor; K is the roll coefficient; z is the axial coordinate; δ r The thickness of the boundary layer of the moving disk; Re r is the Reynolds number; C qr is the radial flow coefficient; Q is the flow rate of the dynamic and static chamber;
[0047] Given the rotor speed ω and flow rate Q; select the boundary layer height coefficie...
PUM
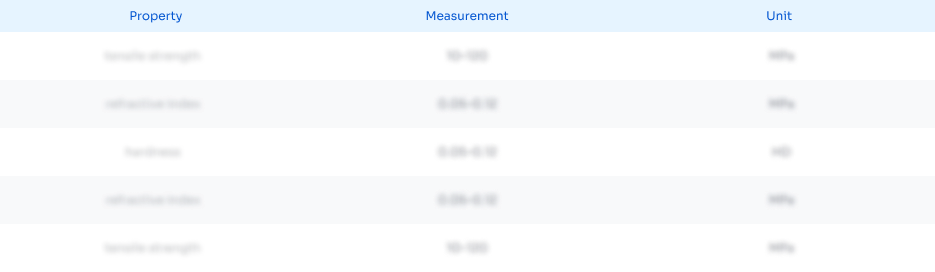
Abstract
Description
Claims
Application Information

- R&D Engineer
- R&D Manager
- IP Professional
- Industry Leading Data Capabilities
- Powerful AI technology
- Patent DNA Extraction
Browse by: Latest US Patents, China's latest patents, Technical Efficacy Thesaurus, Application Domain, Technology Topic, Popular Technical Reports.
© 2024 PatSnap. All rights reserved.Legal|Privacy policy|Modern Slavery Act Transparency Statement|Sitemap|About US| Contact US: help@patsnap.com