Coke oven hydrogen utilization method and system
A coke oven and hydrogen technology, applied in the field of coal coke ovens, can solve the problems of reducing tar yield, reducing benefits, and wasting energy by cracking macromolecular coal tar, so as to promote targeted hydrogenation reactions, improve coke oven productivity, and improve The effect of coking benefit
- Summary
- Abstract
- Description
- Claims
- Application Information
AI Technical Summary
Problems solved by technology
Method used
Image
Examples
Embodiment 1
[0059] Such as figure 2 and 4 As shown, the coke oven hydrogen utilization system described in this embodiment is a system in which the duct 4 is arranged on the other side of the carbonization chamber riser 6; Pipe channel 4; the rising pipe 6 is provided with a flap valve 7; the other end of the coke oven carbonization chamber 1 on the side of the rising pipe 6 of the raw gas outlet is provided with a raw gas inlet and outlet, and the inlet and outlet are connected to the high temperature valve 2 , the high temperature valve 2 is externally connected to the raw gas pipe channel, the pipe channel 4 is arranged side by side parallel to the coke oven carbonization chamber 1, the pipe channel is connected to the high temperature valve 2 in a three-way type, and the high temperature valve 2 is connected to its corresponding coke oven carbonization chamber 1. A catalyst fixed bed 8 is provided in the conduit 4 and / or at the top of the carbonization chamber 1 and / or in the riser ...
Embodiment 2
[0061] Such as image 3 and 5 As shown, the coke oven hydrogen utilization system described in this embodiment is a system in which the pipes and channels 4 are arranged on the same side of the carbonization chamber riser; The inlet and outlet, the inlet and outlet are connected to the inside of the high-temperature valve 2 through a three-way connection at the root of the outlet of the raw gas riser pipe assembly, and the outside of the high-temperature valve 2 is connected to the raw gas pipeline. A catalyst fixed bed 8 is arranged in the canal 4 and / or at the top of the carbonization chamber 1 and / or in the riser 6; the advantage of this embodiment is that it can well solve the technical transformation problem of the existing coke oven without changing the top carbonization of the coke oven. Chamber structure.
Embodiment 3
[0063] Such as figure 2 and 6 As shown, the pipe channel 4 is connected with the carbonization chamber 1 of the coke oven by using the existing furnace top carbonization chamber hole 5 to connect the connecting pipe 3, so that the connecting pipe 3 can be successfully solved for the technical transformation of the technical solution of the present invention for the existing coke oven, and its advantages It is not necessary to renovate the existing coke oven, and use the hole on the top of the carbonization chamber of the existing coke oven to connect the pipes and channels, and increase the length of the raw gas process, so as to increase the reaction time.
[0064] Further, when the coke oven carbonization chamber 1 is provided with a raw gas inlet and outlet at the other end of the raw gas outlet on the side of the rising pipe 6, the high-temperature valve 2 is connected to the corresponding coke oven carbonization chamber 1 through the furnace top carbonization chamber hol...
PUM
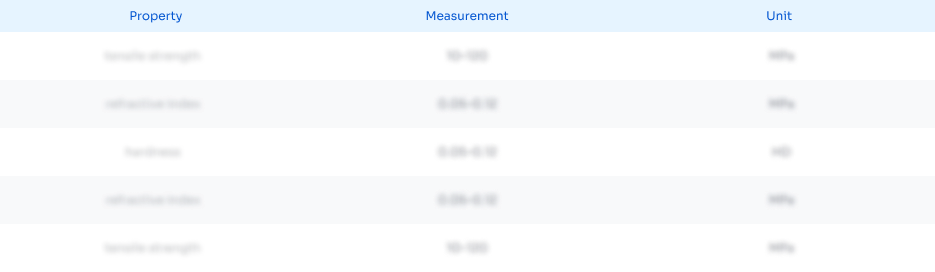
Abstract
Description
Claims
Application Information

- R&D
- Intellectual Property
- Life Sciences
- Materials
- Tech Scout
- Unparalleled Data Quality
- Higher Quality Content
- 60% Fewer Hallucinations
Browse by: Latest US Patents, China's latest patents, Technical Efficacy Thesaurus, Application Domain, Technology Topic, Popular Technical Reports.
© 2025 PatSnap. All rights reserved.Legal|Privacy policy|Modern Slavery Act Transparency Statement|Sitemap|About US| Contact US: help@patsnap.com