Bias working point automatic control system based on temperature drift compensation
An automatic control system and offset working point technology, which is applied in the transmission system, electromagnetic wave transmission system, optics, etc., can solve the problem of link performance deterioration, the pilot method cannot achieve stable working point, and it is difficult to meet high-precision arbitrary offset Work point stability requirements and other issues
- Summary
- Abstract
- Description
- Claims
- Application Information
AI Technical Summary
Problems solved by technology
Method used
Image
Examples
Embodiment Construction
[0027] Embodiments of the present invention are described in detail below, examples of which are shown in the drawings, wherein the same or similar reference numerals designate the same or similar elements or elements having the same or similar functions throughout. The embodiments described below by referring to the figures are exemplary and are intended to explain the present invention and should not be construed as limiting the present invention.
[0028] see figure 1 , figure 1 It is a structural schematic diagram of the bias operating point automatic control system 100 based on temperature drift compensation in the present invention. The present invention provides an automatic bias operating point control system 100 based on temperature drift compensation, including a laser 10, a modulator 20, a coupling optical splitter 30, a first detector 40, a second detector 50, and a feedback loop module 60 and a temperature monitoring module 70, the laser 10 is connected to the o...
PUM
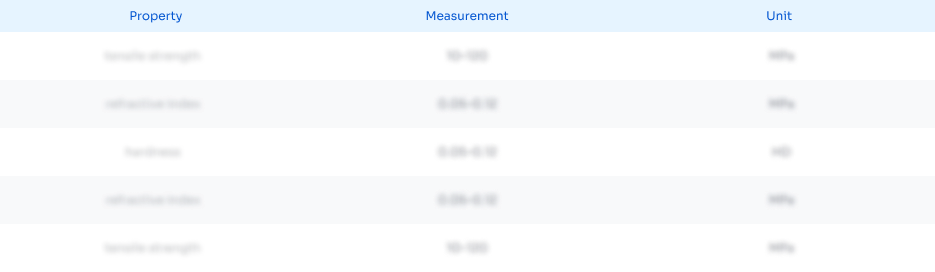
Abstract
Description
Claims
Application Information

- R&D Engineer
- R&D Manager
- IP Professional
- Industry Leading Data Capabilities
- Powerful AI technology
- Patent DNA Extraction
Browse by: Latest US Patents, China's latest patents, Technical Efficacy Thesaurus, Application Domain, Technology Topic, Popular Technical Reports.
© 2024 PatSnap. All rights reserved.Legal|Privacy policy|Modern Slavery Act Transparency Statement|Sitemap|About US| Contact US: help@patsnap.com