A kind of anti-nodulation high-sulfur non-quenched and tempered steel smelting process
A non-quenched and tempered steel, anti-nodulation technology, used in the improvement of process efficiency, furnace, electric furnace, etc., can solve the problems of poor stability of the pouring curve, fluctuation of the liquid level of the mold, slag inclusion under the skin of the rolled material, etc., to reduce the product The effect of scrapping, smooth pouring curve and no fluctuation of liquid level
- Summary
- Abstract
- Description
- Claims
- Application Information
AI Technical Summary
Problems solved by technology
Method used
Image
Examples
Embodiment 1
[0030] An anti-nodulation high-sulfur non-quenched and tempered steel, the smelted steel components are carbon 0.40%-0.45%, silicon 0.30%-0.50%, manganese 1.20%-1.50%, phosphorus ≤ 0.030%, sulfur 0.035%-0.075%, Chromium ≤0.25%, Nickel ≤0.25%, Copper ≤0.20%, Aluminum 0.010%-0.040%, Vanadium 0.06%-0.10%, Molybdenum ≤0.25%, Niobium 0.02%-0.04%, Nitrogen 0.0100%-0.0150%, and the rest iron;
[0031] The smelting process is;
[0032] (1) Electric furnace smelting controls the carbon content of the tapped steel, the carbon is controlled at 0.08% to 0.25%, and the tapped temperature is required to be greater than 1600° C. (the tapped temperature of embodiment 1 is between 1610-1622° C.). The phosphorus requirement at the end of electric furnace smelting is ≤0.018%, and slag is strictly prohibited in the tapping process to ensure that the finished product phosphorus is ≤0.020%.
[0033] Add 120kg of aluminum block / furnace to the deoxidation process of electric furnace tapping, add al...
PUM
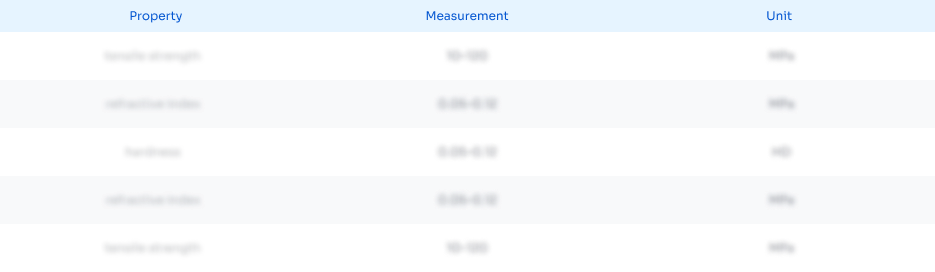
Abstract
Description
Claims
Application Information

- Generate Ideas
- Intellectual Property
- Life Sciences
- Materials
- Tech Scout
- Unparalleled Data Quality
- Higher Quality Content
- 60% Fewer Hallucinations
Browse by: Latest US Patents, China's latest patents, Technical Efficacy Thesaurus, Application Domain, Technology Topic, Popular Technical Reports.
© 2025 PatSnap. All rights reserved.Legal|Privacy policy|Modern Slavery Act Transparency Statement|Sitemap|About US| Contact US: help@patsnap.com