Automatic roller replacing equipment for producing composite flow medium
A diversion net, automatic technology, applied in the field of composite diversion net, can solve the problems of manual cutting and replacement, low work efficiency, and inability to realize the continuity of the production line, so as to ensure continuous winding work and improve work efficiency , the effect of saving working time
- Summary
- Abstract
- Description
- Claims
- Application Information
AI Technical Summary
Problems solved by technology
Method used
Image
Examples
Embodiment 1
[0070] Such as figure 1 , figure 2 As shown, an automatic roll changing equipment for composite guide net production, including:
[0071] Switching mechanism 1, the switching mechanism 1 includes a frame 11, a revolving assembly 12 rotatably arranged on the frame 11, and a take-up roller element 13 rotatably arranged on the revolving assembly 12, the revolving assembly 12 along In the circumferential direction, there are winding station 1a, packing station 1b, output station 1c, upper roller station 1d and station to be replaced 1e;
[0072] The driving mechanism 2, the driving mechanism 2 includes an active assembly 21 arranged on the winding station 1a and used to drive the winding roller element 13 to perform a circular rotation to complete the winding work and installed on the frame 11 and a first autorotation assembly 22 for driving the winding roller element 13 to autorotate;
[0073] The winding mechanism 3, the winding mechanism 3 is provided with two groups and sy...
Embodiment 2
[0121] Such as figure 2 As shown, the components that are the same as or corresponding to those in the first embodiment are marked with the corresponding reference numerals in the first embodiment. For the sake of simplicity, only the differences from the first embodiment will be described below. The difference between this embodiment two and embodiment one is:
[0122] further, such as figure 2 As shown, the sealing mechanism 5 includes a second arc-shaped rack 51, the second arc-shaped rack 51 is provided in two groups and is arranged in one-to-one correspondence with the driving gear 221, the second arc-shaped rack 51 is arranged along the rotation direction of the epicyclic assembly 12 and meshed with the driving gear 221 .
[0123] What is worth mentioning here is that by setting the second arc-shaped rack 51, the winding roller element 13 after finishing the winding work is in the process of revolving, and the winding roller element 13 carries out Automatic winding ...
PUM
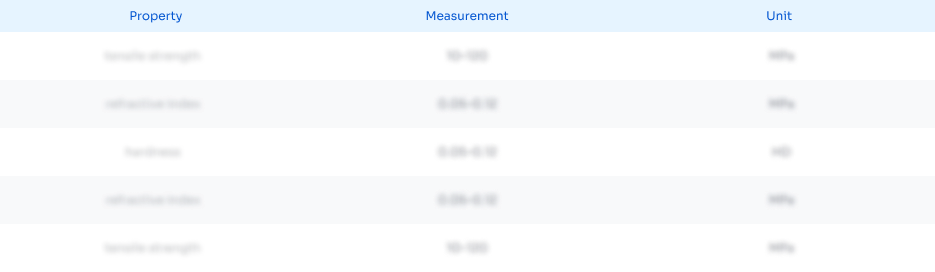
Abstract
Description
Claims
Application Information

- R&D Engineer
- R&D Manager
- IP Professional
- Industry Leading Data Capabilities
- Powerful AI technology
- Patent DNA Extraction
Browse by: Latest US Patents, China's latest patents, Technical Efficacy Thesaurus, Application Domain, Technology Topic, Popular Technical Reports.
© 2024 PatSnap. All rights reserved.Legal|Privacy policy|Modern Slavery Act Transparency Statement|Sitemap|About US| Contact US: help@patsnap.com