Composite vibration energy collector
A vibration energy harvesting and composite technology, applied in the direction of electric components, generators/motors, piezoelectric effect/electrostrictive or magnetostrictive motors, etc., can solve the problem of single output characteristics, achieve wide working bandwidth, Easy to operate and improve work efficiency
- Summary
- Abstract
- Description
- Claims
- Application Information
AI Technical Summary
Problems solved by technology
Method used
Image
Examples
Embodiment Construction
[0022] The present invention will be further described below in conjunction with accompanying drawing.
[0023] Such as Figure 1-Figure 4 As shown, a composite vibration energy harvester includes a shell 1, end caps 7 are fixed on the upper and lower ends of the shell 1, and at least three depth adjustment mechanisms 2 are evenly distributed along the circumferential direction on the circumferential wall of the shell. The number of mechanisms can be three, four, six or eight, etc. The inner end of the depth adjustment mechanism 2 is fixedly connected with a piezoelectric beam 3, and the inner end of the piezoelectric beam 3 is fixedly connected with an elastic membrane 4, and the elastic membrane 4 The upper and lower sides of the housing are fixedly connected with a moving magnet 5, and a frictional electricity generating mechanism 6 is provided between the two moving magnets and the end cover on the same side, and an induction coil 8 is provided on the outer periphery of th...
PUM
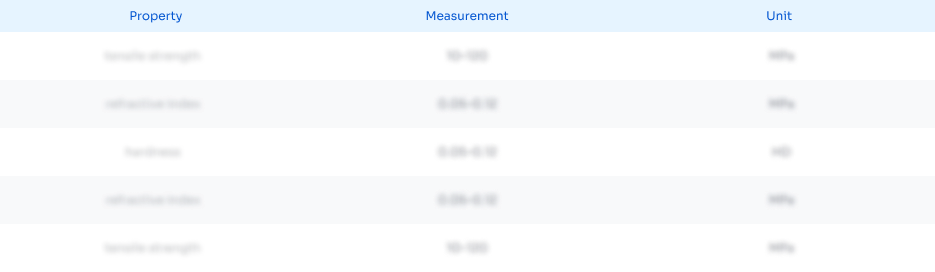
Abstract
Description
Claims
Application Information

- R&D Engineer
- R&D Manager
- IP Professional
- Industry Leading Data Capabilities
- Powerful AI technology
- Patent DNA Extraction
Browse by: Latest US Patents, China's latest patents, Technical Efficacy Thesaurus, Application Domain, Technology Topic, Popular Technical Reports.
© 2024 PatSnap. All rights reserved.Legal|Privacy policy|Modern Slavery Act Transparency Statement|Sitemap|About US| Contact US: help@patsnap.com