Control method of wing-body joint gap distribution based on measured data
A technology of measured data and distributed control, applied in the direction of comprehensive factory control, special data processing application, airframe, etc., to achieve the effect of truly reflecting entity characteristics, enhancing detailed description, improving assembly quality and production efficiency
- Summary
- Abstract
- Description
- Claims
- Application Information
AI Technical Summary
Problems solved by technology
Method used
Image
Examples
Embodiment Construction
[0079] In order to better understand the technical content of the present invention, specific embodiments are given together with the attached drawings for description as follows.
[0080] combine figure 1 , the present invention refers to the wing-body butt joint gap distribution control technology based on measured data, including the following steps:
[0081] First, the original point cloud data of the wing and the point cloud data of the central wing box are obtained respectively by photogrammetry and scanner.
[0082] Firstly, paste coded points and marked points on the four sides of the wing-body joint of the aircraft, use photogrammetry technology to obtain the coordinate information of the coded points and marked points on it to establish a scanning control field, and then use the scanner to scan the wing and the central wing box respectively to obtain Point cloud data, refine the point cloud data to the control field established by photographic measurement, and enhan...
PUM
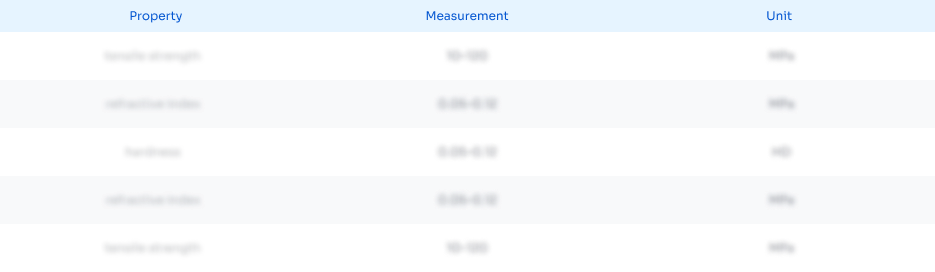
Abstract
Description
Claims
Application Information

- Generate Ideas
- Intellectual Property
- Life Sciences
- Materials
- Tech Scout
- Unparalleled Data Quality
- Higher Quality Content
- 60% Fewer Hallucinations
Browse by: Latest US Patents, China's latest patents, Technical Efficacy Thesaurus, Application Domain, Technology Topic, Popular Technical Reports.
© 2025 PatSnap. All rights reserved.Legal|Privacy policy|Modern Slavery Act Transparency Statement|Sitemap|About US| Contact US: help@patsnap.com