Inchworm bionic structure based on magnetic drive flexible film drivers and manufacturing process
- Summary
- Abstract
- Description
- Claims
- Application Information
AI Technical Summary
Problems solved by technology
Method used
Image
Examples
Embodiment Construction
[0031] The present invention will be described in detail below in conjunction with the accompanying drawings.
[0032] Such as figure 1 As shown, a magnetically driven biomimetic inchworm structure based on a magnetically driven flexible thin film driver includes a top layer of silicone membrane 1 with a certain thickness, a foot structure 2 is provided under the silicone membrane 1, and a silicone membrane 1 is provided under the head and abdomen. There is a magnetically driven flexible film driver 3, the magnetically driven flexible film driver 3, and the foot structure 2 are bonded to the silicone mold 1 through an adhesive material 4, and the magnetic poles of the magnetically driven flexible film driver 3 on the head and abdomen are opposite.
[0033] The silica gel film 1 adopts elastomers such as silica gel or polyurethane, and the foot structure 2 adopts elastomers such as silica gel or polyurethane; the adhesive material 4 adopts silica gel adhesive or silica gel glue...
PUM
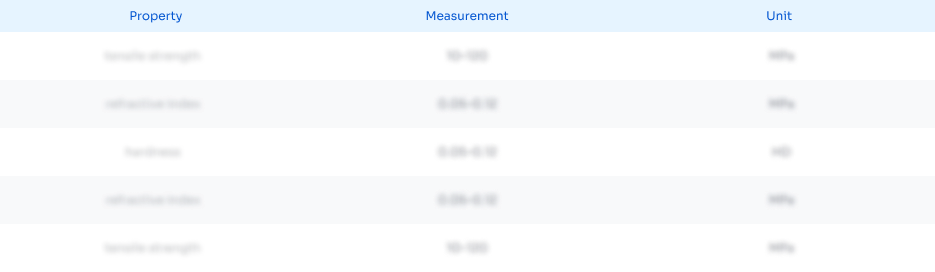
Abstract
Description
Claims
Application Information

- R&D
- Intellectual Property
- Life Sciences
- Materials
- Tech Scout
- Unparalleled Data Quality
- Higher Quality Content
- 60% Fewer Hallucinations
Browse by: Latest US Patents, China's latest patents, Technical Efficacy Thesaurus, Application Domain, Technology Topic, Popular Technical Reports.
© 2025 PatSnap. All rights reserved.Legal|Privacy policy|Modern Slavery Act Transparency Statement|Sitemap|About US| Contact US: help@patsnap.com