Satisfaction optimization prediction fault-tolerant control method for double-three-level inverter
A three-level inverter, fault-tolerant control technology, applied in electrical components, AC power input to DC power output, output power conversion devices, etc., can solve the problem of small number of redundant switch states, weak topology fault tolerance, Increase equipment volume and other issues to achieve the effect of strong fault tolerance, strong operability, and low harmonic distortion rate
- Summary
- Abstract
- Description
- Claims
- Application Information
AI Technical Summary
Problems solved by technology
Method used
Image
Examples
Embodiment 1
[0047] Embodiment 1, with reference to figure 1 —10, a kind of dual three-level inverter satisfaction optimization predictive fault-tolerant control method, its steps are,
[0048] (1) Open the stator winding of the motor, and the two ends of the stator winding are powered by two identical inverters, and the two inverters share the same set of DC bus to form a common bus dual three-level topology;
[0049] (2) When an open-circuit fault occurs in a switching device, the maximum output voltage of the inverter drops to half of the original value, and the range of voltage jumps controlled by the inverter is set within Vdc / 2. The available switching states of the inner hexagon of the flat topology synthesize the reference voltage vector;
[0050] (3) Taking the current following performance as the main control target of the dual-inverter system and establishing a three-phase current satisfactory error function to optimize the aforementioned reference voltage vector;
[0051] (4)...
Embodiment 2
[0063] Embodiment 2, a kind of satisfactory optimal predictive fault-tolerant control method for dual three-level inverters described in Embodiment 1, in order to perform satisfactory optimal fault-tolerant control by operating dual three-level inverters through the MPC controller, assuming w(k) =w(k+1), establish the dynamic mathematical model of the open-winding asynchronous motor with the stator current and the rotor flux linkage as the state variables under the two-phase stationary coordinate system,
[0064]
[0065] In the formula: i sα ,i sβ Respectively, the stator current α, β components in the coordinate system (A); λ rα ,λ rβ Respectively, the component (A) of the rotor flux linkage α and β coordinate system; u sα ,u sβ Respectively, the stator voltage α, β components in the coordinate system (V); L m is the mutual inductance (H); T r =L r / R r , is the rotor electromagnetic time constant; k r =L m / L r ,r o =R s +R r k r 2 ,δ=1-L m 2 / L s / L ...
Embodiment 3
[0071] Embodiment 3, a kind of dual three-level inverter satisfactory optimization prediction fault-tolerant control method described in Embodiment 2, the described three-phase current satisfaction error function is the following formula:
[0072]
[0073] Where: Δi=i * -i(k+1); δ is the maximum allowable ring width of current following;
[0074] The figure below is the judgment diagram of current following satisfaction. The present invention sets [0, δ] as the satisfactory interval. When the current following deviation |Δi| is within this interval, u i = 0, indicating that the current following has achieved a satisfactory effect, when the current following deviation exceeds this range, u i =1, indicating that its following performance is not good, the attached picture Figure 9 It is the judgment diagram of current following satisfaction.
PUM
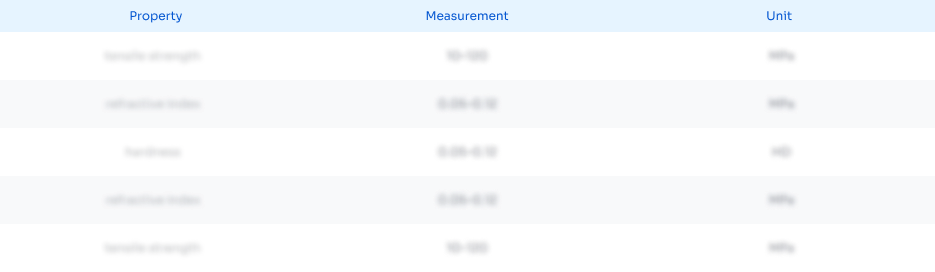
Abstract
Description
Claims
Application Information

- Generate Ideas
- Intellectual Property
- Life Sciences
- Materials
- Tech Scout
- Unparalleled Data Quality
- Higher Quality Content
- 60% Fewer Hallucinations
Browse by: Latest US Patents, China's latest patents, Technical Efficacy Thesaurus, Application Domain, Technology Topic, Popular Technical Reports.
© 2025 PatSnap. All rights reserved.Legal|Privacy policy|Modern Slavery Act Transparency Statement|Sitemap|About US| Contact US: help@patsnap.com