Method and system for determining residual stress and residual elimination effect of material
A technology of residual stress and determination method, applied in the direction of analyzing materials, using sonic/ultrasonic/infrasonic waves for material analysis, force/torque/work measuring instruments, etc. Achieve the effect of accurate measurement and accurate measurement of residual stress
- Summary
- Abstract
- Description
- Claims
- Application Information
AI Technical Summary
Problems solved by technology
Method used
Image
Examples
Embodiment Construction
[0100] The following will clearly and completely describe the technical solutions in the embodiments of the present invention with reference to the accompanying drawings in the embodiments of the present invention. Obviously, the described embodiments are only some, not all, embodiments of the present invention. Based on the embodiments of the present invention, all other embodiments obtained by persons of ordinary skill in the art without making creative efforts belong to the protection scope of the present invention.
[0101] At present, the measurement of residual stress mainly adopts the same method as the measurement of principal stress of material, but the principal stress of material is relatively large, and the trend of change and distribution is more obvious. Therefore, the current method can accurately measure the principal stress of material. However, the residual stress of the material is small, and the change and distribution trend are not obvious. Therefore, the c...
PUM
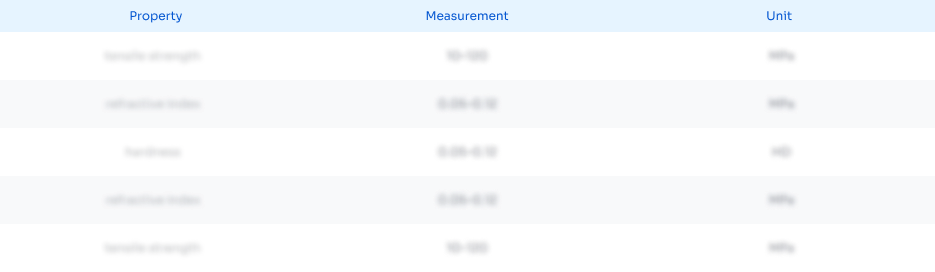
Abstract
Description
Claims
Application Information

- R&D
- Intellectual Property
- Life Sciences
- Materials
- Tech Scout
- Unparalleled Data Quality
- Higher Quality Content
- 60% Fewer Hallucinations
Browse by: Latest US Patents, China's latest patents, Technical Efficacy Thesaurus, Application Domain, Technology Topic, Popular Technical Reports.
© 2025 PatSnap. All rights reserved.Legal|Privacy policy|Modern Slavery Act Transparency Statement|Sitemap|About US| Contact US: help@patsnap.com