Metal component flaw detection screening equipment
A technology for screening equipment and metal parts, applied in the field of metal parts flaw detection and screening equipment, can solve the problems of reducing production efficiency, slow detection speed, and inability to efficiently achieve synchronization of production and detection, and achieve the effect of speeding up production efficiency and reducing scrap rate
- Summary
- Abstract
- Description
- Claims
- Application Information
AI Technical Summary
Problems solved by technology
Method used
Image
Examples
Embodiment Construction
[0014] All features disclosed in this specification, or steps in all methods or processes disclosed, can be combined in any way, except for mutually exclusive features and or steps.
[0015] Combine below Figure 1-4 The present invention is described in detail, and for convenience of description, the orientations mentioned below are now stipulated as follows: figure 1 The up, down, left, right, front and back directions of the projection relationship itself are the same.
[0016] A flaw detection and screening device for metal parts of the device of the present invention includes a body 10, a conveying chamber 75 is provided in the body 10, a detection chamber 76 is provided on the left side of the conveying chamber 75, and a classification chamber is provided on the left side of the detection chamber 76. cavity 77, a power cavity 78 is provided on the rear side of the detection cavity 76, an analysis system 70 is fixed on the left side of the body 10, a hydraulic pump 69 is...
PUM
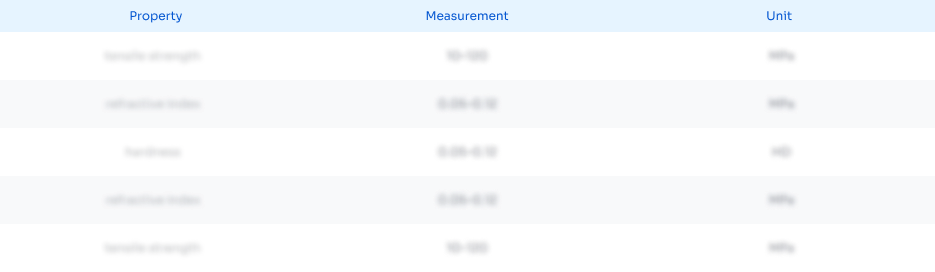
Abstract
Description
Claims
Application Information

- R&D Engineer
- R&D Manager
- IP Professional
- Industry Leading Data Capabilities
- Powerful AI technology
- Patent DNA Extraction
Browse by: Latest US Patents, China's latest patents, Technical Efficacy Thesaurus, Application Domain, Technology Topic, Popular Technical Reports.
© 2024 PatSnap. All rights reserved.Legal|Privacy policy|Modern Slavery Act Transparency Statement|Sitemap|About US| Contact US: help@patsnap.com