An integrated rocket fairing with bearing and noise reduction and its design method
A design method and technology of fairings, which are applied in aerospace safety/emergency devices, thermal protection devices of aerospace vehicles, etc., can solve problems such as encroaching on the space of fairings, environmental excess of acoustic covering layers, threats to fairing satellites, etc., and achieve enhanced Sound insulation ability, improvement of environmental comfort, and effect of reducing internal noise
- Summary
- Abstract
- Description
- Claims
- Application Information
AI Technical Summary
Problems solved by technology
Method used
Image
Examples
Embodiment 1
[0039] like figure 1 As shown, the present application provides a load-carrying and noise-reducing integrated rocket fairing, including: a fairing main body 1 and a resonator 2 arranged on the inner surface of the fairing main body 1; the fairing main body 1 includes a cylindrical section and an arc section, The cylinder section and the arc section are connected together, and the inside of the fairing main body 1 is hollow, and the fairing main body 1 includes two layers of panels 3 and a honeycomb sandwich core 4 arranged between the two layers of panels 3; the honeycomb sandwich core 4 has a core , the core is connected by a plurality of honeycomb cells, and the plurality of honeycomb cells are evenly arranged, and the honeycomb cells are filled with porous sound-absorbing materials 5, effectively utilizing the internal space of the honeycomb sandwich core 4, and enhancing the sound insulation of the honeycomb sandwich core 4 performance. The porous sound-absorbing material...
Embodiment 2
[0050] like Figure 4 As shown, the present application provides a design method for carrying a noise reduction integrated rocket fairing, which design method includes the following steps:
[0051] Step S1, designing the main body of the fairing to obtain four basic variables of the main body of the fairing.
[0052] like Figure 5 As shown, the method of designing the fairing main body includes the following steps:
[0053] Step S110, establishing a hypothesis for the fairing main body.
[0054]Assumptions are established for the main body of the fairing: the panel is a single-layer thin plate; the honeycomb sandwich core does not bear normal stress; the coupling effect between antisymmetric and symmetric deformation is ignored;
[0055] Step S120, on the basis of the above assumptions, establish four basic variables of the fairing body design.
[0056] Specifically, the four basic variables are: first, the panel thickness t f ; Second, the honeycomb sandwich height t c...
PUM
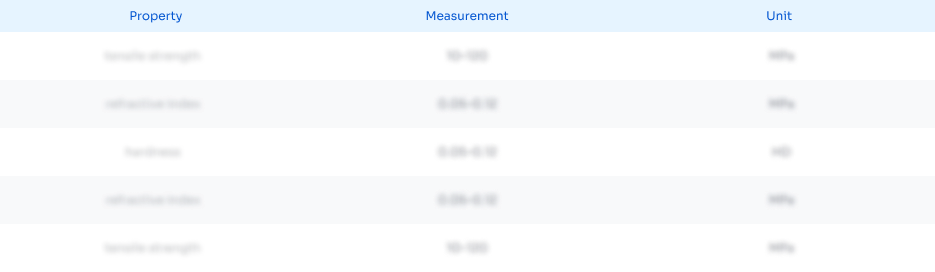
Abstract
Description
Claims
Application Information

- R&D
- Intellectual Property
- Life Sciences
- Materials
- Tech Scout
- Unparalleled Data Quality
- Higher Quality Content
- 60% Fewer Hallucinations
Browse by: Latest US Patents, China's latest patents, Technical Efficacy Thesaurus, Application Domain, Technology Topic, Popular Technical Reports.
© 2025 PatSnap. All rights reserved.Legal|Privacy policy|Modern Slavery Act Transparency Statement|Sitemap|About US| Contact US: help@patsnap.com