Oil-free screw structure and method for adjusting gap of synchronous rotors thereof
An adjustment method and rod structure technology, which is applied in the direction of elastic fluid rotary piston type/oscillating piston type pump combination, rotary piston type pump, rotary piston type machinery, etc., can solve the problem of increasing energy consumption and increasing blank cost , complex adjustment methods and other issues, to achieve the effect of high automation level and fast adjustment
- Summary
- Abstract
- Description
- Claims
- Application Information
AI Technical Summary
Problems solved by technology
Method used
Image
Examples
Embodiment 1
[0030] An oil-free screw structure, including a male rotor 1 and a female rotor 2, and also includes a controller 3, a first servo motor 4, a second servo motor 5, a first servo driver 6, a second servo driver 7, the first The servo motor 4 is connected to the first rotating shaft 8 of the male rotor 1, the second servo motor 5 is connected to the second rotating shaft 9 of the female rotor 2, and the first servo motor 4 and the second servo motor 5 are respectively provided with a second A position detection device 10 and a second position detection device 11, the first position detection device 10 and the first servo motor 4 are electrically connected to the first servo drive 6, the second position detection device 11 and the second servo motor 5 are all electrically connected with the second servo driver 7, and the first servo driver 6 and the second servo driver 7 are all connected in communication with the controller 3; the controller 3 can be a PLC controller 3, and the f...
Embodiment 2
[0035] A method for adjusting the clearance of synchronous rotors with an oil-free screw structure, comprising the following steps:
[0036] (1) Through the first servo driver 6 and the second servo driver 7, the controller 3 controls one of the male and female rotors 1, 2 to be stationary and the other to rotate slowly, and the torque T1 of the servo motor corresponding to the moving rotor is set to be smaller than that corresponding to the stationary rotor The torque T2 of the servo motor, in this embodiment, the torque T2 of the servo motor corresponding to the fixed rotor is set to 70% to 100% of its rated value, and 100% of its rated value can be selected, and the torque T2 of the servo motor corresponding to the moving rotor is set. The torque T1 is 1% to 10% of its rated value, and 5% of its rated value can be selected. The speed V1 of the moving rotor slowly rotates is 1 circle / minute to 2 circles / minute, and 1 circle / minute can be selected;
[0037] (2) The controller...
PUM
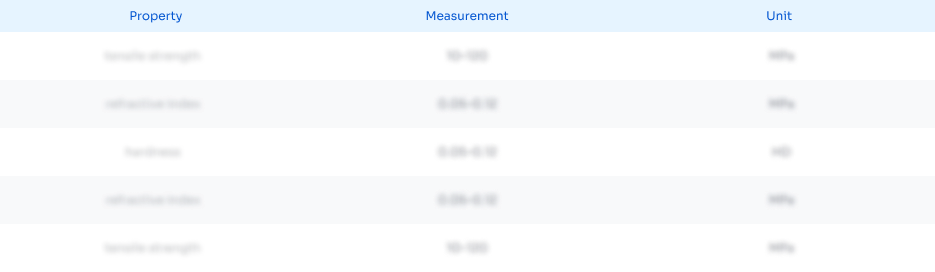
Abstract
Description
Claims
Application Information

- R&D Engineer
- R&D Manager
- IP Professional
- Industry Leading Data Capabilities
- Powerful AI technology
- Patent DNA Extraction
Browse by: Latest US Patents, China's latest patents, Technical Efficacy Thesaurus, Application Domain, Technology Topic, Popular Technical Reports.
© 2024 PatSnap. All rights reserved.Legal|Privacy policy|Modern Slavery Act Transparency Statement|Sitemap|About US| Contact US: help@patsnap.com