A coupling press-fitting device and press-fitting method
A press-fitting device and coupling technology, applied in metal processing equipment, metal processing, manufacturing tools, etc., can solve the problems of increased bushing cost, multiple rework, dissatisfaction, etc., to improve the quality of press-fit and press-fit Efficiency, guaranteed installation requirements, additional cost savings
- Summary
- Abstract
- Description
- Claims
- Application Information
AI Technical Summary
Problems solved by technology
Method used
Image
Examples
Embodiment 2
[0056] The difference from Embodiment 1 is that in this embodiment, one end of the elastic member is fixedly connected to the press-fitting member 16 , and the other end is in direct contact with the end surface of the coupling 2 during press-fitting. In this structure, the elastic member can be a rubber block, a spring leaf (not shown in the figure), etc., and a second installation groove (not shown in the figure) that opens toward the coupling 2 is arranged on the pressing part 16 , the elastic member is installed in the second installation groove, and in a natural state, the elastic member protrudes a certain distance from the second installation groove.
[0057] After being pressed into place, the elastic piece can be compressed into the second installation groove as a whole, so that the end surface of the pressing piece 16 is in contact with the end surface of the coupling 2, and the height of the limit groove 22 is used to limit the distance between the end surface of the...
PUM
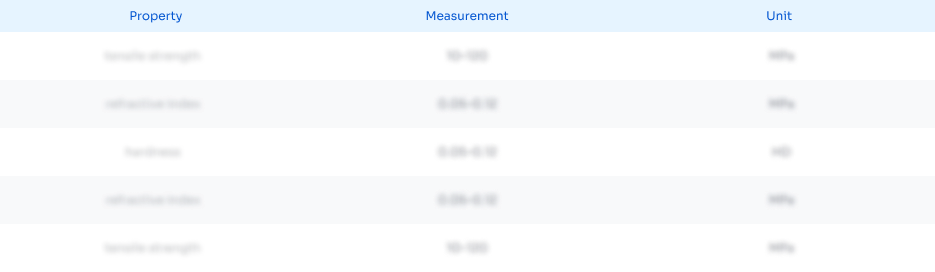
Abstract
Description
Claims
Application Information

- Generate Ideas
- Intellectual Property
- Life Sciences
- Materials
- Tech Scout
- Unparalleled Data Quality
- Higher Quality Content
- 60% Fewer Hallucinations
Browse by: Latest US Patents, China's latest patents, Technical Efficacy Thesaurus, Application Domain, Technology Topic, Popular Technical Reports.
© 2025 PatSnap. All rights reserved.Legal|Privacy policy|Modern Slavery Act Transparency Statement|Sitemap|About US| Contact US: help@patsnap.com