Heat recovery method of washing tower process water
A heat recovery and washing tower technology, applied in the chemical industry, can solve the problems such as the temperature of washing water cannot be removed in time, the effect of process gas washing is affected, and the heat of washing water is wasted, so as to solve the problem of heat balance, reduce maintenance frequency, and improve production. The effect of the rate
- Summary
- Abstract
- Description
- Claims
- Application Information
AI Technical Summary
Problems solved by technology
Method used
Image
Examples
Embodiment Construction
[0027] The following will clearly and completely describe the technical solutions in the embodiments of the present invention with reference to the accompanying drawings in the embodiments of the present invention. Obviously, the described embodiments are only some, not all, embodiments of the present invention.
[0028] refer to figure 1 , a heat recovery method for washing tower process water, comprising the following steps:
[0029] The hot water buffer tank 4 uses the desalinated water F to build the liquid level to normal. As the source of hot water, the hot water G goes out from the bottom of the hot water buffer tank 4 and goes to the hot water circulation pump 5. During normal production, only A small amount of water needs to be added to the tank to maintain the normal liquid level in the hot water buffer tank and the circulation of hot water;
[0030] The inlet of the hot water circulation pump 5 receives the hot water G from the hot water buffer tank 4, pressurizes ...
PUM
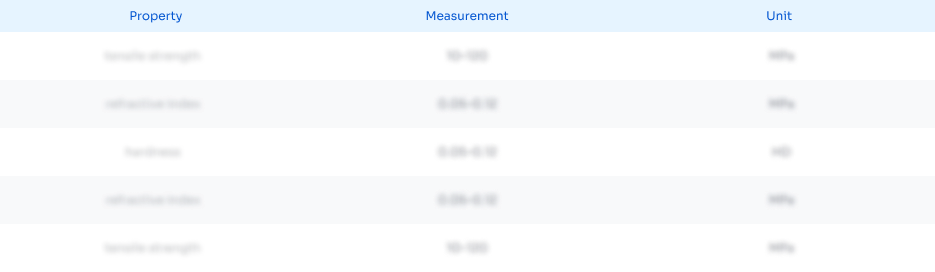
Abstract
Description
Claims
Application Information

- R&D
- Intellectual Property
- Life Sciences
- Materials
- Tech Scout
- Unparalleled Data Quality
- Higher Quality Content
- 60% Fewer Hallucinations
Browse by: Latest US Patents, China's latest patents, Technical Efficacy Thesaurus, Application Domain, Technology Topic, Popular Technical Reports.
© 2025 PatSnap. All rights reserved.Legal|Privacy policy|Modern Slavery Act Transparency Statement|Sitemap|About US| Contact US: help@patsnap.com