A dual-arm collaborative intelligent assembly system based on vision positioning
A visual positioning and assembly system technology, applied in the direction of program-controlled manipulators, metal processing equipment, manipulators, etc., can solve the problems of slow assembly speed and high labor costs, reduce requirements, reduce labor costs, and solve the effect of unable to assemble
- Summary
- Abstract
- Description
- Claims
- Application Information
AI Technical Summary
Problems solved by technology
Method used
Image
Examples
Embodiment Construction
[0036] The following will clearly and completely describe the technical solutions in the embodiments of the present invention with reference to the accompanying drawings in the embodiments of the present invention. Obviously, the described embodiments are some of the embodiments of the present invention, but not all of them. Based on the embodiments of the present invention, all other embodiments obtained by persons of ordinary skill in the art without making creative efforts belong to the protection scope of the present invention.
[0037] The embodiment of the present invention discloses a dual-arm collaborative intelligent assembly system based on visual positioning, which includes two robotic arms and two cameras, wherein the first camera is fixed on the end effector of the active robotic arm to photograph the module base; the second camera is fixed on the outside of the active manipulator; the end effector of the slave manipulator is an automatic screwdriver. Calibration,...
PUM
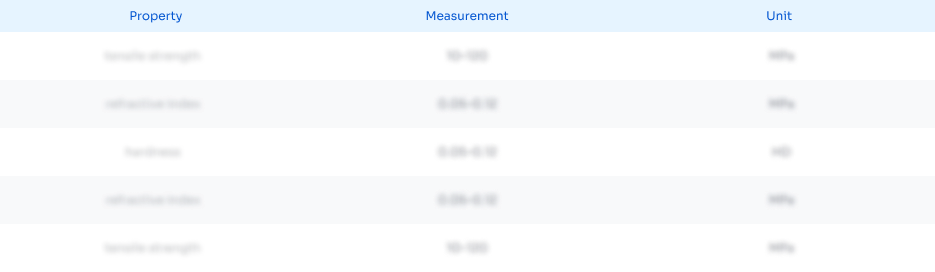
Abstract
Description
Claims
Application Information

- R&D Engineer
- R&D Manager
- IP Professional
- Industry Leading Data Capabilities
- Powerful AI technology
- Patent DNA Extraction
Browse by: Latest US Patents, China's latest patents, Technical Efficacy Thesaurus, Application Domain, Technology Topic, Popular Technical Reports.
© 2024 PatSnap. All rights reserved.Legal|Privacy policy|Modern Slavery Act Transparency Statement|Sitemap|About US| Contact US: help@patsnap.com