A kind of aqueous dispersion agent and its preparation method and application
A water-based dispersant and solvent technology, applied in the field of materials, can solve the problems of poor dispersion and instability, and achieve the effect of not easy to settle, strong force, not easy to fall off and be replaced
- Summary
- Abstract
- Description
- Claims
- Application Information
AI Technical Summary
Problems solved by technology
Method used
Image
Examples
Embodiment 1
[0042] Mix 200g benzyl methacrylate, 140g methyl ethyl ketone and 30g isopropanol uniformly to obtain premix A; mix 25g potassium methacrylate with 200g water and 25g isopropanol uniformly to obtain premix B; take 30.5g Butanone and 7 g of azobiscyanovaleric acid were mixed and stirred until dissolved to obtain premix C; then 20 g of butanone and 4.3 g of azobiscyanovaleric acid were mixed and stirred until dissolved to obtain premix D.
[0043] Put nitrogen into the reaction flask equipped with a condensing reflux device, add 300g of water and 18.2g of isopropanol, heat to 90-100°C and reflux for half an hour to remove air; then premix A, B and premix C, and simultaneously Slowly add to the reaction bottle for reaction; the reaction temperature is 90°C, after about 5.5 hours of reaction, add the premixed solution D into the reaction bottle, and react for about 1 hour, and stop the reaction after detecting that the amount of residual monomer is less than 5%; put the reaction bo...
Embodiment 2
[0045] To prepare a premix, mix 175g benzyl methacrylate, 140g methyl ethyl ketone and 30g isopropanol to obtain premix A; mix 50g potassium methacrylate with 200g water and 25g isopropanol to obtain premix B Take 30.5g butanone and 7g azobiscyanovaleric acid and mix and stir until dissolved to obtain premix C; then take 20g butanone and 4.3g azobiscyanovaleric acid and mix and stir until dissolved to obtain premix D.
[0046] Infuse nitrogen into the reaction flask equipped with a condensing reflux device, add 300g of water and 18.2g of isopropanol, heat to 90-100°C and reflux for half an hour to remove air; then premix A, B and premix C, and simultaneously Slowly add to the reaction bottle for reaction; the reaction temperature is 60°C, after about 5.5 hours of reaction, add the premix D into the reaction bottle, and react for about 1 hour, and stop the reaction after detecting that the amount of residual monomer is less than 5%, and obtain an aqueous Dispersant B.
Embodiment 3
[0048] To prepare a premix, mix 182.3g benzyl methacrylate, 140g butanone and 30g isopropanol uniformly to obtain a premix A; mix 42.7g potassium methacrylate with 200g water and 25g isopropanol to obtain a premix Mixture B; take 30.5g butanone and 7g of azobiscyanovaleric acid and mix and stir until dissolved to obtain premix C; then take 20g of butanone and 4.3g of azobiscyanovaleric acid and mix and stir until dissolved to obtain a premix d.
[0049] Infuse nitrogen into the reaction flask equipped with a condensing reflux device, add 300g of water and 18.2g of isopropanol, heat to 90-100°C and reflux for half an hour to remove air; then premix A, B and premix C, and simultaneously Slowly add to the reaction bottle for reaction; the reaction temperature is 100°C, after about 5.5 hours of reaction, add the premix D into the reaction bottle, and react for about 1 hour, and stop the reaction after detecting that the amount of residual monomer is less than 5%; put the reaction bo...
PUM
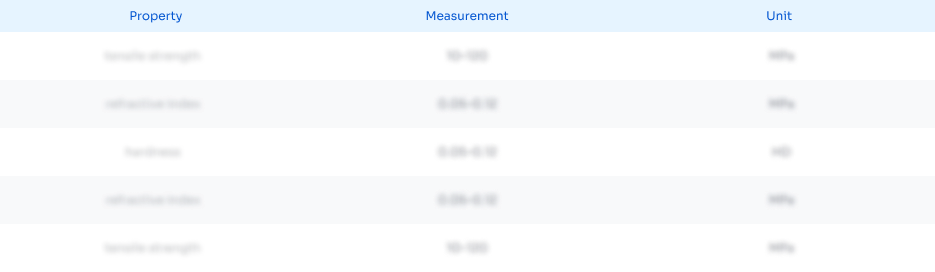
Abstract
Description
Claims
Application Information

- R&D
- Intellectual Property
- Life Sciences
- Materials
- Tech Scout
- Unparalleled Data Quality
- Higher Quality Content
- 60% Fewer Hallucinations
Browse by: Latest US Patents, China's latest patents, Technical Efficacy Thesaurus, Application Domain, Technology Topic, Popular Technical Reports.
© 2025 PatSnap. All rights reserved.Legal|Privacy policy|Modern Slavery Act Transparency Statement|Sitemap|About US| Contact US: help@patsnap.com