Robot mechanical arm
A technology of robots and mechanical arms, applied in the field of industrial robots, can solve the problems of inability to complete welding tasks, affecting welding quality, affecting welding efficiency, etc., to improve welding efficiency and quality, improve welding scope, and improve welding efficiency and quality. Effect
- Summary
- Abstract
- Description
- Claims
- Application Information
AI Technical Summary
Problems solved by technology
Method used
Image
Examples
Embodiment Construction
[0023] The following will clearly and completely describe the technical solutions in the embodiments of the present invention with reference to the accompanying drawings in the embodiments of the present invention. Obviously, the described embodiments are only some, not all, embodiments of the present invention. Based on the embodiments of the present invention, all other embodiments obtained by persons of ordinary skill in the art without making creative efforts belong to the protection scope of the present invention.
[0024] see Figure 1-6 , a robot mechanical arm, including a fixed base 1, a servo motor and a precision harmonic reducer, the top of the fixed base 1 is movably connected with a rotating base 2, and the upper left part of the rotating base 2 is fixedly equipped with a fixed servo motor 7, and the fixed servo The extension shaft at the right end of the motor 7 is fixedly equipped with connecting arm 8, the bottom of connecting arm 8 right side is fixedly insta...
PUM
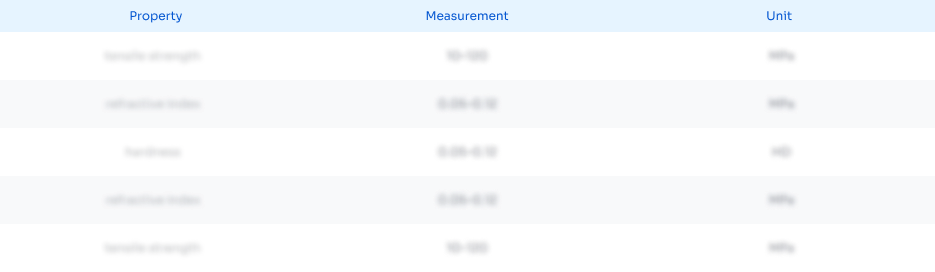
Abstract
Description
Claims
Application Information

- Generate Ideas
- Intellectual Property
- Life Sciences
- Materials
- Tech Scout
- Unparalleled Data Quality
- Higher Quality Content
- 60% Fewer Hallucinations
Browse by: Latest US Patents, China's latest patents, Technical Efficacy Thesaurus, Application Domain, Technology Topic, Popular Technical Reports.
© 2025 PatSnap. All rights reserved.Legal|Privacy policy|Modern Slavery Act Transparency Statement|Sitemap|About US| Contact US: help@patsnap.com