Expandable vibration damping type self-adaptive instrument mounting platform
A technology for installing platforms and instrument mounting plates, which is applied in the direction of supporting machines, machine platforms/supports, non-rotational vibration suppression, etc., and can solve the problem of not optimizing the stress environment of instruments and equipment from a dynamic point of view, failing to reach the design carrying capacity, and local load-bearing Reduced capacity and other issues, to achieve the effect of saving production cost and cycle, reducing mold investment, and improving carrying capacity
- Summary
- Abstract
- Description
- Claims
- Application Information
AI Technical Summary
Problems solved by technology
Method used
Image
Examples
Embodiment 1
[0043] Such as figure 1 , in this embodiment, an expandable vibration-damping adaptive instrument installation platform based on a two-stage split structure is disclosed, including: a load-bearing base I1, a load-bearing base II2, and an instrument installation plate I5. Among them, the tops of the load-bearing base I1 and the load-bearing base II2 are respectively connected with the instrument mounting plate I5; the load-bearing base I1 and the load-bearing base II2 are connected through the The installation holes of the missile body are connected with the stringers or the main structure on the structure shell of the missile body to ensure sufficient connection strength; the instrument installation plate I5 is connected with at least one instrument through the instrument installation holes set on the instrument installation plate I5 .
[0044] Preferably, the expandable vibration-damping adaptive instrument installation platform based on the two-stage split structure further...
Embodiment 2
[0051] Such as Figure 4 , in this embodiment, an expandable vibration-reducing adaptive instrument installation platform based on a three-level split structure is disclosed, including: load-bearing base III6, load-bearing base IV7, load-bearing base V8, Bearing base Ⅵ9, instrument mounting plate Ⅱ10 and instrument mounting plate Ⅲ11. Among them, the tops of load-bearing base III6 and load-bearing base IV7 are respectively connected with the instrument installation board II10; the tops of load-bearing base V8 and load-bearing base VI9 are respectively connected with the instrument installation board III11; The bottoms of load-bearing base IV7, load-bearing base V8 and load-bearing base VI9 are connected with stringers or the main structure on the shell of the projectile body structure, so as to realize the strengthening of transverse and longitudinal connection stiffness, and at the same time, it is used to strengthen the gap between the bases. The constraint rigidity improve...
PUM
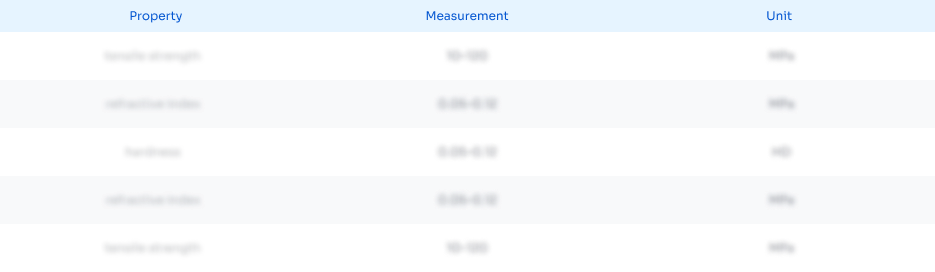
Abstract
Description
Claims
Application Information

- Generate Ideas
- Intellectual Property
- Life Sciences
- Materials
- Tech Scout
- Unparalleled Data Quality
- Higher Quality Content
- 60% Fewer Hallucinations
Browse by: Latest US Patents, China's latest patents, Technical Efficacy Thesaurus, Application Domain, Technology Topic, Popular Technical Reports.
© 2025 PatSnap. All rights reserved.Legal|Privacy policy|Modern Slavery Act Transparency Statement|Sitemap|About US| Contact US: help@patsnap.com