Simple calculation method for radial maximum displacement of diaphragm wall in excavation stage
A calculation method and maximum displacement technology, applied in calculation, design optimization/simulation, data processing applications, etc., can solve problems such as unfavorable engineering promotion, high requirements for theoretical calculation skills, and difficulties in radial displacement of ground-connected walls, etc., to achieve calculation Simple, high-precision results
- Summary
- Abstract
- Description
- Claims
- Application Information
AI Technical Summary
Problems solved by technology
Method used
Image
Examples
Embodiment
[0039] Such as Figure 1-3 As shown, a simple calculation method for the maximum radial displacement of the ground connecting wall at the excavation stage includes the following steps:
[0040] Step S1: Establish a finite element model in the excavation stage of the ground connecting wall. The finite element model is a grooved body. The finite element model includes ground connecting wall 1, bottom plate 2, inner lining 3 and core filler 4. Ground connecting wall 1 is a semi-cylinder The bottom of the finite element model is provided with a bottom plate 2, and the inner side of the ground connecting wall 1 is closely fitted with an inner lining 3. The finite element model is filled with a filler 4, and there is an arch 6 above the finite element model. The top of 1 is the cap beam 5.
[0041] Step S2: Simplify the ground connecting wall 1 into a cylindrical curved surface, select a cylindrical curved surface on the ground connecting wall 1 and establish a curved surface coordinate ...
PUM
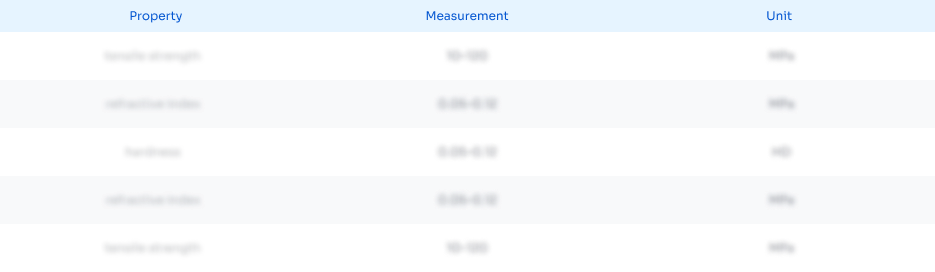
Abstract
Description
Claims
Application Information

- R&D
- Intellectual Property
- Life Sciences
- Materials
- Tech Scout
- Unparalleled Data Quality
- Higher Quality Content
- 60% Fewer Hallucinations
Browse by: Latest US Patents, China's latest patents, Technical Efficacy Thesaurus, Application Domain, Technology Topic, Popular Technical Reports.
© 2025 PatSnap. All rights reserved.Legal|Privacy policy|Modern Slavery Act Transparency Statement|Sitemap|About US| Contact US: help@patsnap.com