Fixed shaft type full-moving rudder surface mounting structure
An installation structure, fixed-axis technology, applied in transportation and packaging, aircraft parts, aircraft control, etc., can solve the problem of aircraft flutter speed and flight quality affecting the life of structural parts, increased rudder surface rotational friction, and rudder surface control. Clearance nonlinearity and other problems, to achieve the beneficial effects of aircraft flutter speed and flight quality, good installation consistency, and stable control clearance of the rudder surface
- Summary
- Abstract
- Description
- Claims
- Application Information
AI Technical Summary
Problems solved by technology
Method used
Image
Examples
Embodiment Construction
[0022] The embodiments will be described in detail below in conjunction with the accompanying drawings.
[0023] figure 1 It is a schematic diagram of the installation structure of the fixed-axis full-motion rudder surface, figure 2 for figure 1 sectional view of image 3 A schematic diagram of the shaft structure. See attached figure 1 To attach image 3 , the installation structure of the fixed-axis full-motion rudder surface includes a rotating shaft 1, a beam 3 and a rocker arm 6, the rotating shaft 1 is fixed on the supporting structure, the beam 3 is sleeved on the rotating shaft 1 and locked, and the rocking arm 6 is fixed On the beam 3, the steering gear 7 operates the rocker arm 6 to drive the beam 3 to rotate around the rotating shaft 1, and the beam 3 is set on the rotating shaft 1 as a double fulcrum.
[0024] Considering that the rotating shaft 1 and the rudder surface are generally supported by double fulcrums, the fulcrum load of the fuselage section clos...
PUM
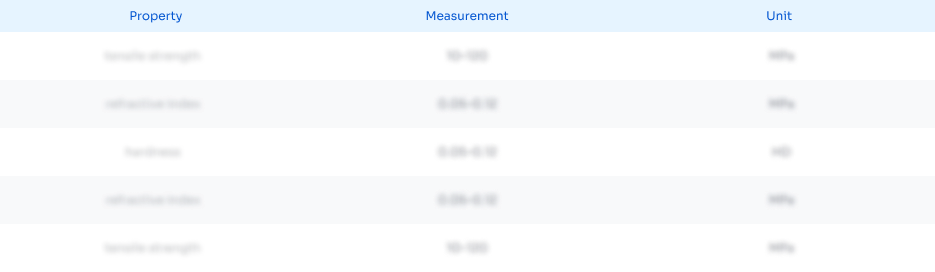
Abstract
Description
Claims
Application Information

- R&D
- Intellectual Property
- Life Sciences
- Materials
- Tech Scout
- Unparalleled Data Quality
- Higher Quality Content
- 60% Fewer Hallucinations
Browse by: Latest US Patents, China's latest patents, Technical Efficacy Thesaurus, Application Domain, Technology Topic, Popular Technical Reports.
© 2025 PatSnap. All rights reserved.Legal|Privacy policy|Modern Slavery Act Transparency Statement|Sitemap|About US| Contact US: help@patsnap.com