Industrial robot space pose measuring mechanism and measuring method based on stay wire rotation sensor
A technology of industrial robots and rotation sensors, applied in manipulators, manufacturing tools, etc., can solve the problems of high price, large space occupation, and high cost, and achieve the effects of strong environmental applicability, simple structure, and low cost
- Summary
- Abstract
- Description
- Claims
- Application Information
AI Technical Summary
Problems solved by technology
Method used
Image
Examples
Embodiment Construction
[0035] Such as figure 1 As shown, an industrial robot space pose measurement mechanism based on a cable rotation sensor includes: a base 1 and a test platform 7, the base 1 is equipped with a rotating platform 2, and the rotating platform 2 is installed in different directions There are three wire-drawing encoders 3 and three steering mechanisms 4, and the test platform 7 is equipped with three wire-drawing adapter mechanisms 6, and the wires 5 in the three wire-drawing encoders 3 are adapted to the respective wires through the respective steering mechanisms 4 Organization 6 is connected.
[0036] Such as Figure 2-3 As shown, the test body is modeled:
[0037] Meaning of symbols: on the rotary platform 2, the virtual equivalent base point at which the pull wires 5 of the three pull wire encoders 3 pass through their respective steering mechanisms 4 is marked as A ji (j=1,2,3; i represents the number of rotations of the rotating platform 2, i=0 in the initial condition), th...
PUM
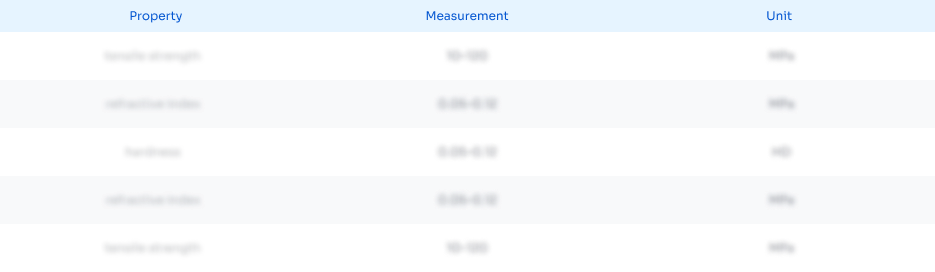
Abstract
Description
Claims
Application Information

- Generate Ideas
- Intellectual Property
- Life Sciences
- Materials
- Tech Scout
- Unparalleled Data Quality
- Higher Quality Content
- 60% Fewer Hallucinations
Browse by: Latest US Patents, China's latest patents, Technical Efficacy Thesaurus, Application Domain, Technology Topic, Popular Technical Reports.
© 2025 PatSnap. All rights reserved.Legal|Privacy policy|Modern Slavery Act Transparency Statement|Sitemap|About US| Contact US: help@patsnap.com