Modeling method for NX Klingelnberg cycloid bevel gear
A modeling method and technology of bevel gears, applied in geometric CAD and other directions, can solve problems such as inconvenient processing of tooth end face rounding, model tooth shape distortion, and low modeling efficiency
- Summary
- Abstract
- Description
- Claims
- Application Information
AI Technical Summary
Problems solved by technology
Method used
Image
Examples
Embodiment Construction
[0076] The following will clearly and completely describe the technical solutions in the embodiments of the present invention with reference to the accompanying drawings in the embodiments of the present invention. Obviously, the described embodiments are only some, not all, embodiments of the present invention. Based on the embodiments of the present invention, all other embodiments obtained by persons of ordinary skill in the art without making creative efforts belong to the protection scope of the present invention.
[0077] see Figure 1~2 , in an embodiment of the present invention, an NX Klingenberg cycloidal bevel gear modeling method,
[0078] Step S1: Write the Klingenberg cycloid bevel gear function:
[0079] Basic input parameters: large gear big end indexing circle diameter D02=580, driving gear teeth number z1=12, driven gear teeth number z2=41, helix angle βm=35, shaft intersection angle Σ=90, driving gear tooth height variation coefficient Xh =0.44, driving wh...
PUM
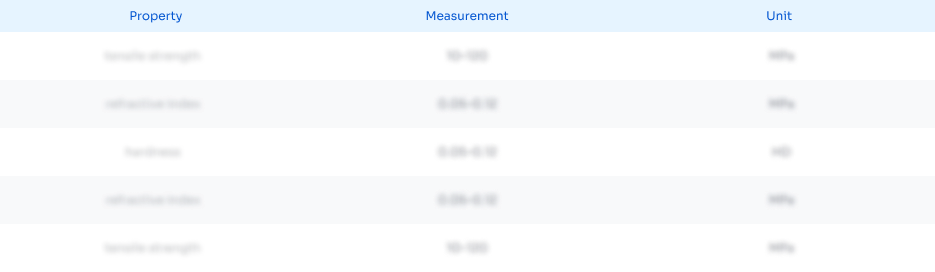
Abstract
Description
Claims
Application Information

- R&D Engineer
- R&D Manager
- IP Professional
- Industry Leading Data Capabilities
- Powerful AI technology
- Patent DNA Extraction
Browse by: Latest US Patents, China's latest patents, Technical Efficacy Thesaurus, Application Domain, Technology Topic, Popular Technical Reports.
© 2024 PatSnap. All rights reserved.Legal|Privacy policy|Modern Slavery Act Transparency Statement|Sitemap|About US| Contact US: help@patsnap.com