Snakelike arm robot changing rigidity based on inner and outer core particle blocking
A technology of variable stiffness and core particles, which is applied in the field of snake-arm robots, can solve problems such as difficulty in robot control accuracy and load capacity, difficulty in robot control, and super-redundancy of robots, and achieve a wide range of stiffness changes, reduced quantity, and reduced The effect of weight and volume
- Summary
- Abstract
- Description
- Claims
- Application Information
AI Technical Summary
Problems solved by technology
Method used
Image
Examples
Embodiment 1
[0077] Embodiment 1: The displacement driving part is set on the side away from the extension direction of the main body of the serpentine arm. The first motor 26 drives the first nut sliding block 28 to drive the inner core 4 to move linearly and repeatedly. The second motor 27 drives the first nut sliding block 28 Thereby driving the outer core 5 to move repeatedly in a straight line. Preferably, during the task of the robot, the first motor 26 and the second motor 27 are respectively controlled so that the first nut slider 28 can push the inner core 4 to move forward, and the second nut slider 29 can push the outer core 5 forward. Action, the mutual cooperation of the two motors can realize the relative movement of the inner core 4 and the outer core 5 to complete the extension. In the reset process, the first motor 26 and the second motor 27 respectively control the first nut sliding block 28 and the second nut sliding block 29 to pull back the inner core 4 and the outer c...
Embodiment 2
[0080] Embodiment 2: Embodiment 1 provides a component that can control the robot to extend and pull back. The difference between Embodiment 1 and Embodiment 2 is: preferably, the silk thread 6 is fixedly connected to the head of the core body 4, and the silk thread 6 It passes through between the inner core 4 and the outer core 5 interlayer, and is connected with the winding reel. The spinning reel and the motor 22 are fixedly mounted on the first nut slide block 28 by means of a connecting piece such as a screw or using a third connecting piece like a bracket in two known ways in the mechanical field. This embodiment provides an embodiment in which the pull-cord component and the displacement driving component are integrated on the pull-cord drive device 2 . The rotating shaft of the reel is fixedly connected with the output end of the motor 22 through connecting pieces such as screws. Preferably, the wire reel and the motor 22 are located on the rear side of the first nut ...
PUM
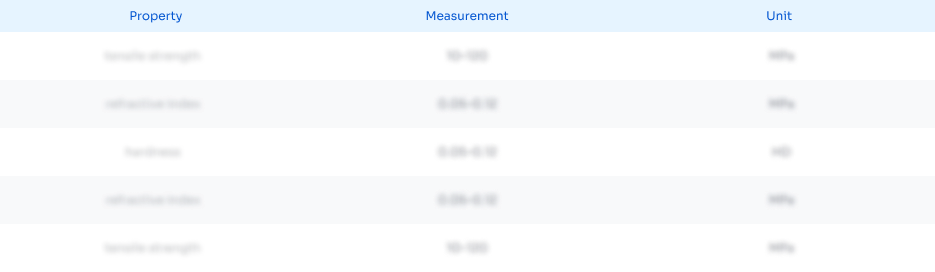
Abstract
Description
Claims
Application Information

- Generate Ideas
- Intellectual Property
- Life Sciences
- Materials
- Tech Scout
- Unparalleled Data Quality
- Higher Quality Content
- 60% Fewer Hallucinations
Browse by: Latest US Patents, China's latest patents, Technical Efficacy Thesaurus, Application Domain, Technology Topic, Popular Technical Reports.
© 2025 PatSnap. All rights reserved.Legal|Privacy policy|Modern Slavery Act Transparency Statement|Sitemap|About US| Contact US: help@patsnap.com