Marine tail vane simulation training system
A stern rudder and naval technology, applied in the field of naval stern rudder simulation training system, can solve the problems that theoretical assessment cannot represent all, no assessment of operational adaptability, incomplete assessment of trainees, etc., so as to prolong service life and reduce occurrences. The effect of the probability of failure
- Summary
- Abstract
- Description
- Claims
- Application Information
AI Technical Summary
Problems solved by technology
Method used
Image
Examples
Embodiment 1
[0032] See attached figure 1 , a naval tail rudder simulation training system, comprising a first oil cylinder a, a second oil cylinder b, a drive plate c, a first tail rudder d, a second tail rudder e, a first drive rod f, a second drive rod g and workbench m.
[0033] Both the first tail rudder d and the second tail rudder e are vertically rotatable and installed on the workbench m, specifically, the top rotating shaft d-1 of the first rudder d is rotatably installed on the workbench m, and the second The top rotating shaft e-1 of the rudder e is rotatably installed on the workbench m, the top rotating shaft d-1 of the first rudder d is connected to the first connecting arm d-2, and the top rotating shaft e-1 of the first rudder e is connected to There is a second connecting arm e-2, the outer end of the first connecting arm d-2 is hinged with one end of the first driving rod f, the other end of the first driving rod f is hinged at the tail end of the driving plate c, the s...
Embodiment 2
[0037] The driving system of the ship rudder simulation training system is introduced below.
[0038] See attached figure 2 , the drive system adopts a dual power system structure, including the first electric oil pump 5, the second electric oil pump 14, the first check valve 7, the second check valve 17, the first electromagnetic reversing valve 9, the second electromagnetic reversing valve 28. The first electromagnetic switch valve 10, the second electromagnetic switch valve 20, the balance valve 19, the first electromagnetic proportional overflow valve 23, the second electromagnetic proportional overflow valve 12, the third electromagnetic proportional overflow valve 20, the first manual On-off valve 29, the second manual on-off valve 30 and the oil tank.
[0039] The oil inlet of the first electric oil pump 5 is connected with the oil tank, the oil outlet of the first electric oil pump 5 is connected to the inlet of the first one-way valve 7, and the outlet of the first ...
Embodiment 3
[0051] On the basis of the second embodiment, further, the oil inlet of the first electric oil pump 5 is further connected with a first filter 3 , and the oil outlet of the first electric oil pump is also connected with a second filter 6 . The oil inlet of the second electric oil pump 14 is also connected with a third filter, and the oil outlet of the second electric oil pump is also connected with a fourth filter 16 . The impurities in the oil are filtered out through the filter, reducing the probability of failure of hydraulic components and prolonging the service life of hydraulic components.
PUM
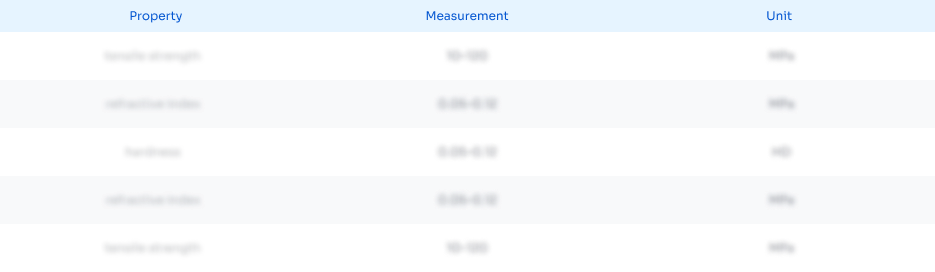
Abstract
Description
Claims
Application Information

- R&D Engineer
- R&D Manager
- IP Professional
- Industry Leading Data Capabilities
- Powerful AI technology
- Patent DNA Extraction
Browse by: Latest US Patents, China's latest patents, Technical Efficacy Thesaurus, Application Domain, Technology Topic, Popular Technical Reports.
© 2024 PatSnap. All rights reserved.Legal|Privacy policy|Modern Slavery Act Transparency Statement|Sitemap|About US| Contact US: help@patsnap.com