A molding machine for pole plate insulating strips with automatic blanking and alignment
A technology of automatic cutting and insulating strips, applied in the field of machinery, can solve the problems of low degree of mechanized production, easy damage to the pole plates and insulating strips, and difficult cathode plates.
- Summary
- Abstract
- Description
- Claims
- Application Information
AI Technical Summary
Problems solved by technology
Method used
Image
Examples
Embodiment 1
[0013] Such as figure 1 The shown is an automatic blanking and alignment plate insulating strip molding machine, including a conveyor belt 1, a centering mechanism 2 and a material detection sensor 3 are installed on both sides of the conveyor belt 1; a lifting device 4 is installed above the conveyor belt 1, and the lifting device 4 A baffle plate 5 is connected; a lower pressing mechanism 6 is installed on both sides of the lifting device 4, and the lower pressing mechanism 6 is connected with a lower pressing block 7, and a groove 8 is formed on the lower pressing block 7, and the groove 8 is connected with a lower pressing mechanism through a spring 16. Mold 9, the first groove 11 that cooperates with insulating strip 10 is formed on the pressing mold 9; Groove 13 ; the upper mold 12 is connected with a jacking mechanism 14 ; the centering mechanism 2 is connected with a centering clamp 15 that cooperates with the insulating strip 10 .
[0014] The material detection sens...
PUM
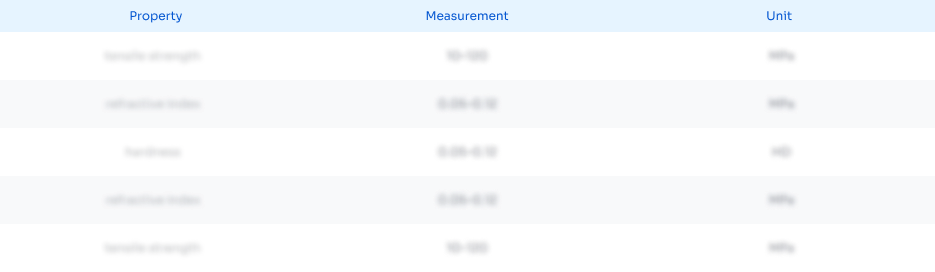
Abstract
Description
Claims
Application Information

- Generate Ideas
- Intellectual Property
- Life Sciences
- Materials
- Tech Scout
- Unparalleled Data Quality
- Higher Quality Content
- 60% Fewer Hallucinations
Browse by: Latest US Patents, China's latest patents, Technical Efficacy Thesaurus, Application Domain, Technology Topic, Popular Technical Reports.
© 2025 PatSnap. All rights reserved.Legal|Privacy policy|Modern Slavery Act Transparency Statement|Sitemap|About US| Contact US: help@patsnap.com