Automatic positioning method for drill rod end straightening
An automatic positioning and drill pipe technology, applied in the control using feedback, program control in sequence/logic controller, electrical program control, etc., can solve the problems of low positioning accuracy, poor straightness and poor consistency of straightening products , to achieve the effect of improved safety and improved positioning accuracy
- Summary
- Abstract
- Description
- Claims
- Application Information
AI Technical Summary
Problems solved by technology
Method used
Image
Examples
Embodiment Construction
[0018] The present invention will be further described below in conjunction with the accompanying drawings and specific embodiments.
[0019] see figure 1 , figure 2 , image 3 , Figure 4 , an automatic positioning method for straightening the end of a drill pipe, is to perform axial and circumferential straightening phase positioning control at the straightening position, wherein:
[0020] Axis control: see figure 1 ,
[0021] The driving system controls the axial conveying roller table 6, and transports the drill pipe 4 from right to left to the straightening area on the conveying roller table, so that the straightening blind area of the drill pipe 4 is fully exposed to the detection field of view of the displacement sensors 2 and 3, and the displacement Sensors 2 and 3 are installed on the measuring frame 15 above the conveying roller table, and the displacement sensors 2 and 3 detect the axial position of the drill pipe 4 and feed back to the controller to output ...
PUM
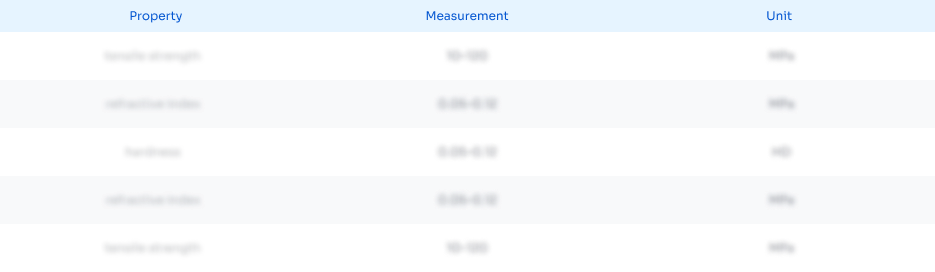
Abstract
Description
Claims
Application Information

- Generate Ideas
- Intellectual Property
- Life Sciences
- Materials
- Tech Scout
- Unparalleled Data Quality
- Higher Quality Content
- 60% Fewer Hallucinations
Browse by: Latest US Patents, China's latest patents, Technical Efficacy Thesaurus, Application Domain, Technology Topic, Popular Technical Reports.
© 2025 PatSnap. All rights reserved.Legal|Privacy policy|Modern Slavery Act Transparency Statement|Sitemap|About US| Contact US: help@patsnap.com