Diesel particulate filter ash cleaning solution and preparation method thereof
A particle trap and cleaning solution technology, which is applied in chemical instruments and methods, detergent compositions, detergent compounding agents, etc., can solve problems such as high maintenance costs, expensive equipment, and the size of the DPF cannot be too large
- Summary
- Abstract
- Description
- Claims
- Application Information
AI Technical Summary
Problems solved by technology
Method used
Image
Examples
Embodiment 1
[0023] This embodiment provides a diesel particulate filter ash cleaning solution, which is composed of the following raw materials in parts by mass:
[0024]
[0025]
[0026] The preparation method of the above-mentioned diesel particulate filter ash cleaning solution comprises the following steps:
[0027] 1) Add surfactant additives, surfactants, ash scavenger, and water into the reactor and heat to 50°C according to the ratio of parts by mass;
[0028] 2) add chelating agent in reactor, and stir;
[0029] 3) Cool down to 20°C, add corrosion inhibitor, defoamer, and dispersant, and stir evenly.
[0030] The DPF was cleaned with the above-mentioned cleaning solution, and the DPF mass change rate before and after cleaning was used as an evaluation standard, and the DPF mass change rate before and after cleaning in Example 1 was 2.5%.
Embodiment 2
[0032] This embodiment provides a diesel particulate filter ash cleaning solution, which is composed of the following raw materials in parts by mass:
[0033]
[0034] The preparation method of the above-mentioned diesel particulate filter ash cleaning solution comprises the following steps:
[0035] 1) Add surfactant additives, surfactants, ash scavenger, and water into the reactor and heat to 70°C according to the ratio of parts by mass;
[0036] 2) add chelating agent in reactor, and stir;
[0037] 3) Cool down to 25°C, add corrosion inhibitor, defoamer, and dispersant, and stir evenly.
[0038] The above-mentioned cleaning solution was used to clean the DPF, and the DPF mass change rate before and after cleaning was used as the evaluation standard, and the DPF mass change rate before and after cleaning in Example 2 was 3.1%.
Embodiment 3
[0040] This embodiment provides a diesel particulate filter ash cleaning solution, which is composed of the following raw materials in parts by mass:
[0041]
[0042] The preparation method of the above-mentioned diesel particulate filter ash cleaning solution comprises the following steps:
[0043] 1) Add surfactant additives, surfactants, ash scavenger, and water into the reactor and heat to 60° C. according to the ratio of parts by mass;
[0044] 2) add chelating agent in reactor, and stir;
[0045] 3) Cool down to 25°C, add corrosion inhibitor, defoamer, and dispersant, and stir evenly.
[0046] The DPF was cleaned with the above-mentioned cleaning solution, and the DPF mass change rate before and after cleaning was used as the evaluation standard, and the DPF mass change rate before and after cleaning in Example 3 was 2.8%.
PUM
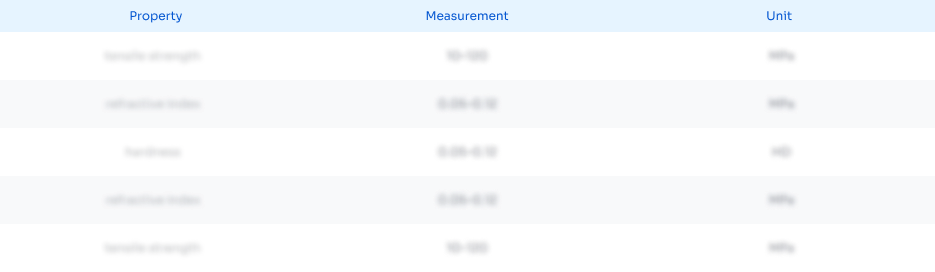
Abstract
Description
Claims
Application Information

- Generate Ideas
- Intellectual Property
- Life Sciences
- Materials
- Tech Scout
- Unparalleled Data Quality
- Higher Quality Content
- 60% Fewer Hallucinations
Browse by: Latest US Patents, China's latest patents, Technical Efficacy Thesaurus, Application Domain, Technology Topic, Popular Technical Reports.
© 2025 PatSnap. All rights reserved.Legal|Privacy policy|Modern Slavery Act Transparency Statement|Sitemap|About US| Contact US: help@patsnap.com