Linear capacitor manufacturing method
A manufacturing method and capacitor technology, which is applied in capacitor manufacturing, capacitors, circuits, etc., can solve problems such as low efficiency, complicated welding process, poor product consistency, etc., and achieve the effect of ensuring high precision and high speed
- Summary
- Abstract
- Description
- Claims
- Application Information
AI Technical Summary
Problems solved by technology
Method used
Image
Examples
Embodiment Construction
[0029] The present invention is further described in conjunction with the following examples.
[0030] Depend on Figure 1 to Figure 11 It can be seen that the method for manufacturing a linear capacitor described in this embodiment includes a frame 1, a vertical plate 11 disposed on the frame 1, a driving element 12 disposed on the vertical plate 11, and an output terminal connected to the driving element 12. The driving sprocket 13, the driven sprocket 14 linked with the driving sprocket 13, the chain 2 set between the driving sprocket 13 and the driven sprocket 14 and the vertical plate 11 for making the chain 2 tight tensioning mechanism;
[0031] The vertical plate 11 is sequentially provided with a capacitor feeding mechanism 4, a laser tangent mechanism 5, a ball welding mechanism 6, an insulating pad sleeve mechanism 7, an electrode sheet feeding and welding mechanism 8, and a discharge mechanism in the moving direction of the chain 2;
[0032] The chain 2 includes a...
PUM
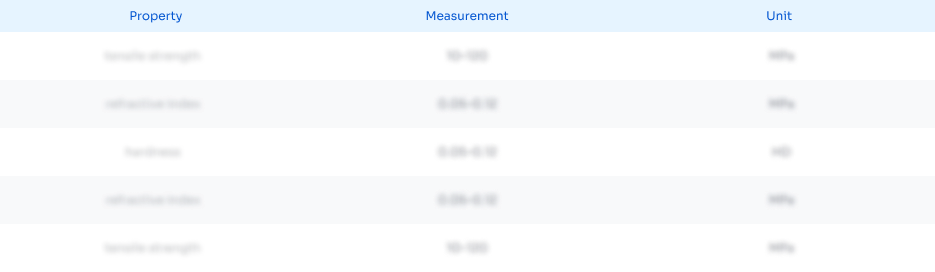
Abstract
Description
Claims
Application Information

- R&D
- Intellectual Property
- Life Sciences
- Materials
- Tech Scout
- Unparalleled Data Quality
- Higher Quality Content
- 60% Fewer Hallucinations
Browse by: Latest US Patents, China's latest patents, Technical Efficacy Thesaurus, Application Domain, Technology Topic, Popular Technical Reports.
© 2025 PatSnap. All rights reserved.Legal|Privacy policy|Modern Slavery Act Transparency Statement|Sitemap|About US| Contact US: help@patsnap.com