Yarn tensioning mechanism for spinning
A tensioning mechanism and yarn technology, applied in the direction of conveying filamentous materials, thin material handling, transportation and packaging, etc., can solve the problems of high tensioning strength, loose yarns, affecting yarn spinning, etc. high intensity effect
- Summary
- Abstract
- Description
- Claims
- Application Information
AI Technical Summary
Problems solved by technology
Method used
Image
Examples
Embodiment 1
[0027] see Figure 1-3 , the present embodiment provides a yarn tensioning mechanism for textiles, comprising a mounting bracket 8 and a guide roller 1, the mounting bracket 8 is a U-shaped structure, the inner cavity of the guide roller 1 is a hollow structure, and the inner cavity of the guide roller 1 There are several hollow sleeves 3 that are evenly spaced in a ring and are radially welded. The connecting shafts 2 are fixedly welded between the tips of the several hollow sleeves 3. The side walls on both sides of the connecting shaft 2 are welded with joints The connecting rods distributed in the axial direction of the shaft 2, the guide roller 1 is rotationally connected with the top of the inner front and rear side walls of the mounting bracket 8 through two connecting rods, and the end of each hollow sleeve 3 away from the connecting shaft 2 is extended to the end of the guide roller 1 The side wall of the inner ring and the radial side wall of the guide roller 1 are p...
Embodiment 2
[0034] see Figure 1-3 , made further improvement on the basis of embodiment 1:
[0035] The outer wall of each I-shaped yarn guide wheel 4 is sleeved with anti-slip rubber sleeves, and the sliding friction force when the I-shaped yarn guide wheels 4 leads are enhanced to prevent skidding by setting the anti-slip rubber sleeves.
[0036] The inner cavity side wall of each sliding insertion hole 11 is embedded with a number of steel balls 12 that are evenly spaced and are rotatably fitted to the outer wall of the extension rod 6 . Sliding resistance when rod 6 slides.
[0037] The major diameter of the inner cavity of each sliding insertion hole 11 is equal to 0.8 times of the major diameter of the inner cavity of each hollow sleeve 3, which prevents the limit magnet block 61 from crossing the inner cavity of the sliding insertion hole 11, thereby preventing the extension rod 6 from breaking away The inner cavity of the hollow sleeve 3.
[0038] Mounting plates 7 are horizon...
PUM
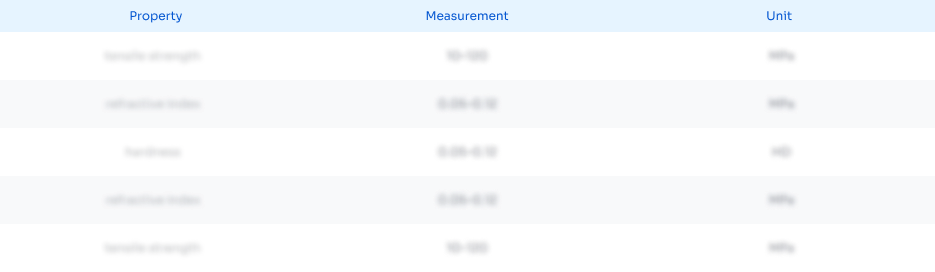
Abstract
Description
Claims
Application Information

- R&D
- Intellectual Property
- Life Sciences
- Materials
- Tech Scout
- Unparalleled Data Quality
- Higher Quality Content
- 60% Fewer Hallucinations
Browse by: Latest US Patents, China's latest patents, Technical Efficacy Thesaurus, Application Domain, Technology Topic, Popular Technical Reports.
© 2025 PatSnap. All rights reserved.Legal|Privacy policy|Modern Slavery Act Transparency Statement|Sitemap|About US| Contact US: help@patsnap.com