Ship lap joint type groove type construction method
A construction method and groove technology, which can be applied to ships and other directions, can solve the problems of large welding workload and welding deformation, and achieve the effects of convenient use, easy debonding, and convenient manufacturing.
- Summary
- Abstract
- Description
- Claims
- Application Information
AI Technical Summary
Problems solved by technology
Method used
Image
Examples
Embodiment Construction
[0027] The specific implementation manners of the present invention will be further described below in conjunction with the drawings and examples. The following examples are only used to illustrate the technical solution of the present invention more clearly, but not to limit the protection scope of the present invention.
[0028] A method for constructing a lap-joint trough of a ship, wherein the bulkhead is a U-shaped trough, comprising the following steps:
[0029] (1) Prepare tire frame tooling 1 specially for U-shaped groove welding, and said tire frame tooling surveys and draws hypothetical center line 2 and horizontal line;
[0030] (2) The U-groove bottom plate is positioned according to the center line and the horizontal line, the width data of the bottom plate is measured to determine the connection point of the side plate, and the angle between the side plate and the bottom plate is determined by the first angle control tool;
[0031] (3) Flat welding is used to we...
PUM
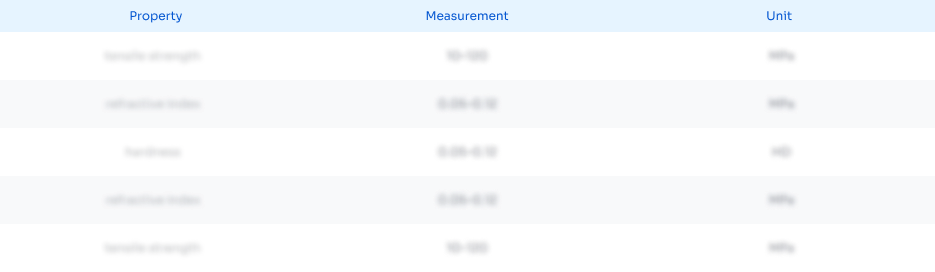
Abstract
Description
Claims
Application Information

- R&D
- Intellectual Property
- Life Sciences
- Materials
- Tech Scout
- Unparalleled Data Quality
- Higher Quality Content
- 60% Fewer Hallucinations
Browse by: Latest US Patents, China's latest patents, Technical Efficacy Thesaurus, Application Domain, Technology Topic, Popular Technical Reports.
© 2025 PatSnap. All rights reserved.Legal|Privacy policy|Modern Slavery Act Transparency Statement|Sitemap|About US| Contact US: help@patsnap.com