Laying method of full-height foam sandwich wing surface laying layer
A layer laying and foaming technology, which is applied in the field of integral molding of composite materials, can solve the problems of complexity, many auxiliary forming tools, and difficulty in laying layers, so as to achieve simple operation, reduce the number of forming tools, and reduce the number of layers and layers. The effect of difficulty
- Summary
- Abstract
- Description
- Claims
- Application Information
AI Technical Summary
Problems solved by technology
Method used
Image
Examples
Embodiment 1
[0057] The wing box section of a certain type of UAV is made of soft skin, soft front and rear beams, and the front, middle and rear three sections of full-height foam are formed at one time by the overall co-curing molding method. The inner profile of the box section is supported by filled full-height foam, and the outer profile is guaranteed by the upper and lower combined molds. There is no gap between the foam and the skeleton and skin. A certain amount of shrinkage is reserved when the foam is machined. Clamped with bolts, molded after curing and formed, polished and trimmed, the quality of the non-destructive testing parts is good, meeting the design index requirements, installed and used, the parts are shown as follows Figure 10 As shown, the steps of laying boxes are as follows Figure 12 shown.
Embodiment 2
[0059] The flap of a certain type of UAV is an integral co-cured structure. During use, the right rear side of the flap was torn in a large area due to collision caused by improper traction. After removing the damaged area, a new full-height foam sandwich was made to restore the structural integrity. Reinforcements are repaired. Reinforcing parts are shown as Figure 13 As shown, the laying steps of reinforcements are as follows Figure 15 shown.
PUM
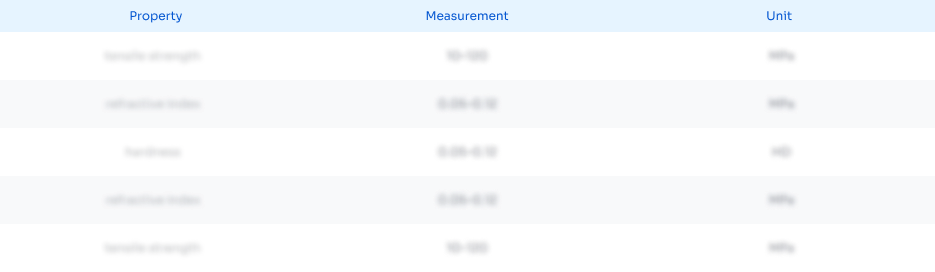
Abstract
Description
Claims
Application Information

- R&D
- Intellectual Property
- Life Sciences
- Materials
- Tech Scout
- Unparalleled Data Quality
- Higher Quality Content
- 60% Fewer Hallucinations
Browse by: Latest US Patents, China's latest patents, Technical Efficacy Thesaurus, Application Domain, Technology Topic, Popular Technical Reports.
© 2025 PatSnap. All rights reserved.Legal|Privacy policy|Modern Slavery Act Transparency Statement|Sitemap|About US| Contact US: help@patsnap.com