A sheet metal forming method for aircraft skin parts with sag
A technology for aircraft skins and parts, which is applied in the field of sheet metal forming with sunken aircraft skin parts, can solve problems such as poor stretch forming mold sticking, and achieve the effects of improving satisfaction, saving mold costs, and avoiding workload
- Summary
- Abstract
- Description
- Claims
- Application Information
AI Technical Summary
Problems solved by technology
Method used
Image
Examples
Embodiment 1
[0028] A sheet metal forming method with sunken aircraft skin parts is characterized in that it comprises the following steps:
[0029] a. According to the size of the part and the drawing die, the block material is cut;
[0030] b. Use the drawing die to stretch the parts through the skin stretching machine;
[0031] c. Roughly cut the shape of the part and drill the positioning pin hole;
[0032] d. Use the partial cover plate and the corresponding punch to suppress the sag on the hydraulic press,
[0033] e. Trim the shape of the part to the theoretical shape.
[0034] The detailed steps of the step a are as follows: the size of the lower block is based on the stretching direction of the skin along the stretching model surface plus a length of 600-700 mm.
[0035] The detailed steps of the step b are as follows: when stretching, part of the cover plate and the bushing for drilling need to be removed, and the parts are stretched and formed by using a drawing die.
[0036...
Embodiment 2
[0040] A sheet metal forming method with sunken aircraft skin parts is characterized in that it comprises the following steps:
[0041] a. According to the size of the part and the drawing die, the block material is cut;
[0042] b. Use the drawing die to stretch the parts through the skin stretching machine;
[0043] c. Roughly cut the shape of the part and drill the positioning pin hole;
[0044] d. Use the partial cover plate and the corresponding punch to suppress the sag on the hydraulic press,
[0045] e. Trim the shape of the part to the theoretical shape.
[0046] The detailed steps of the step a are as follows: the size of the lower block is based on the stretching direction of the skin along the stretching model surface plus a length of 600-700 mm.
[0047] The detailed steps of the step b are as follows: when stretching, part of the cover plate and the bushing for drilling need to be removed, and the parts are stretched and formed by using a drawing die.
[0048...
Embodiment 3
[0051] A sheet metal forming method with sunken aircraft skin parts is characterized in that it comprises the following steps:
[0052] a. According to the size of the part and the drawing die, the block material is cut;
[0053] b. Use the drawing die to stretch the parts through the skin stretching machine;
[0054] c. Roughly cut the shape of the part and drill the positioning pin hole;
[0055] d. Use the partial cover plate and the corresponding punch to suppress the sag on the hydraulic press,
[0056] e. Trim the shape of the part to the theoretical shape.
[0057] The detailed steps of the step a are as follows: the size of the lower block is based on the stretching direction of the skin along the stretching model surface plus a length of 600-700 mm.
[0058] The detailed steps of the step b are as follows: when stretching, part of the cover plate and the bushing for drilling need to be removed, and the parts are stretched and formed by using a drawing die.
[0059...
PUM
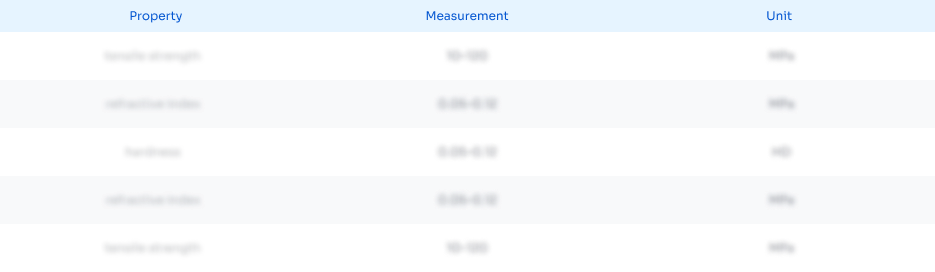
Abstract
Description
Claims
Application Information

- R&D Engineer
- R&D Manager
- IP Professional
- Industry Leading Data Capabilities
- Powerful AI technology
- Patent DNA Extraction
Browse by: Latest US Patents, China's latest patents, Technical Efficacy Thesaurus, Application Domain, Technology Topic, Popular Technical Reports.
© 2024 PatSnap. All rights reserved.Legal|Privacy policy|Modern Slavery Act Transparency Statement|Sitemap|About US| Contact US: help@patsnap.com