Quantitative evaluation method for drilling defects of carbon fiber composite materials
A composite material and defect evaluation technology, which is applied in the field of mechanical processing, can solve problems such as missing and deviation of evaluation results, and achieve the effect of overcoming inaccuracy and realizing strength and life
- Summary
- Abstract
- Description
- Claims
- Application Information
AI Technical Summary
Problems solved by technology
Method used
Image
Examples
Embodiment Construction
[0023] like figure 1 As shown, it is a quantitative evaluation method for drilling quality of carbon fiber composite materials involved in this embodiment. By introducing delamination defects, exit tear defects and exit burr defects in the carbon fiber composite material drilling process, the drilling quality Quantitative evaluation.
[0024] The quantitative evaluation factor Obtained by the following process:
[0025] like figure 2 Shown is the delamination of the processed carbon fiber composite material by ultrasonic scanning, the delamination area is identified by color, and the three-dimensional delamination factor is calculated by the following formula: V nom =p·h·A nom ,
[0026] like image 3 As shown in Fig. 1, the image of the drilling exit is firstly collected, and then the image is processed. The box around the unit area of the hole is taken for image recognition, and the image is first pixelated by using Imagine J software to identify the defects. ...
PUM
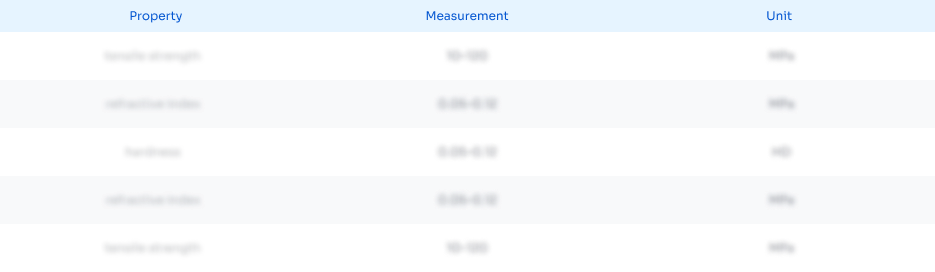
Abstract
Description
Claims
Application Information

- R&D
- Intellectual Property
- Life Sciences
- Materials
- Tech Scout
- Unparalleled Data Quality
- Higher Quality Content
- 60% Fewer Hallucinations
Browse by: Latest US Patents, China's latest patents, Technical Efficacy Thesaurus, Application Domain, Technology Topic, Popular Technical Reports.
© 2025 PatSnap. All rights reserved.Legal|Privacy policy|Modern Slavery Act Transparency Statement|Sitemap|About US| Contact US: help@patsnap.com