Bending process and bending equipment of elevator sill
A technology for sills and elevators, applied in metal processing equipment, elevators in buildings, manufacturing tools, etc., can solve the problems of reduced production efficiency, trouble in welding, position deviation of guides 13, etc., and reduce the defective product rate. , the effect of improving production efficiency
- Summary
- Abstract
- Description
- Claims
- Application Information
AI Technical Summary
Problems solved by technology
Method used
Image
Examples
Embodiment Construction
[0036] The present invention will be described in further detail below in conjunction with the accompanying drawings.
[0037] refer to figure 2 with image 3 , which is a bending process for an elevator sill disclosed by the present invention, comprising the following steps:
[0038] Step 1: plate cutting, the raw material plate is cut by a cutting machine to form a rectangular plate to be processed 1;
[0039] Step 2: Opening folding grooves 2, a total of eleven folding grooves 2 are opened on the upper surface and the lower surface of the plate to be processed 1 by the milling cutter, and one side of the plate to be processed 1 is called a plate edge 11, Each folding groove 2 is parallel to the sheet material edge 11, and the folding groove 2 is a V-shaped groove, and the folding groove 2 is successively named as the first groove 21, the second groove 22, the The third groove 23, the fourth groove 24, the fifth groove 25, the sixth groove 26, the seventh groove 27, the ...
PUM
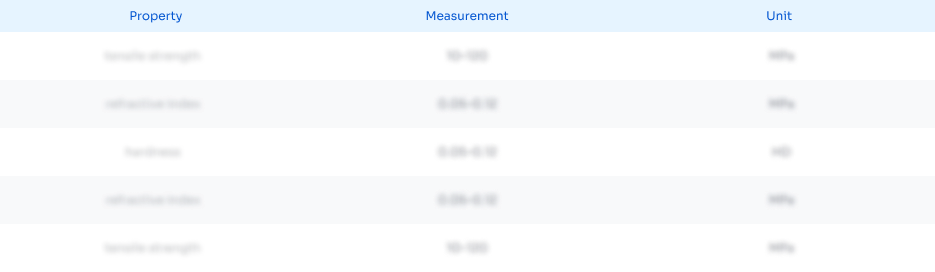
Abstract
Description
Claims
Application Information

- Generate Ideas
- Intellectual Property
- Life Sciences
- Materials
- Tech Scout
- Unparalleled Data Quality
- Higher Quality Content
- 60% Fewer Hallucinations
Browse by: Latest US Patents, China's latest patents, Technical Efficacy Thesaurus, Application Domain, Technology Topic, Popular Technical Reports.
© 2025 PatSnap. All rights reserved.Legal|Privacy policy|Modern Slavery Act Transparency Statement|Sitemap|About US| Contact US: help@patsnap.com