Heaving measurement method with lever arm compensation and suitable for strapdown inertial navigation system
A strapdown inertial navigation and measurement method technology, applied in the field of heave measurement, can solve the problems of long convergence time, easy interference of satellite signals, phase error, etc., to achieve the effect of improving operability
- Summary
- Abstract
- Description
- Claims
- Application Information
AI Technical Summary
Problems solved by technology
Method used
Image
Examples
Embodiment Construction
[0035] The present invention will be described in more detail below in conjunction with the accompanying drawings.
[0036] A heave measurement method with lever arm compensation suitable for a strapdown inertial navigation system, comprising the following steps:
[0037] Step 1. Given the initial navigation parameters (at t=0 moment): the initial alignment of the strapdown inertial navigation system obtains the initial pitch attitude angle θ(0), the initial roll attitude angle γ(0), the initial yaw angle ψ( 0), the main heading angle ζ(0); the projection of the lever arm error between the installation point of the SINS and the center of gravity of the ship on the carrier coordinate system The projection of the lever arm error between the heave observation point M and the center of gravity of the ship on the carrier coordinate system
[0038] Step 2. The system sets the sampling period h, and collects the output signals of the gyroscope and accelerometer on the three axes ...
PUM
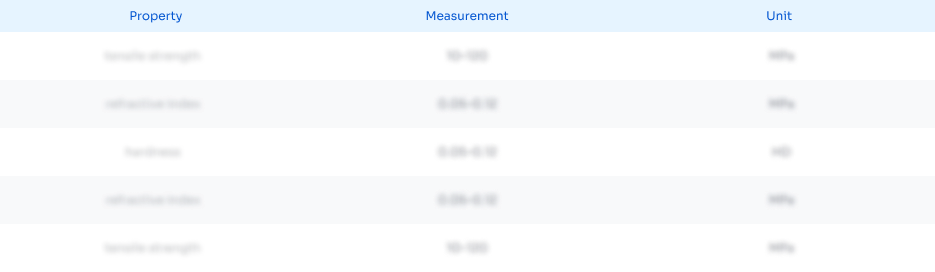
Abstract
Description
Claims
Application Information

- Generate Ideas
- Intellectual Property
- Life Sciences
- Materials
- Tech Scout
- Unparalleled Data Quality
- Higher Quality Content
- 60% Fewer Hallucinations
Browse by: Latest US Patents, China's latest patents, Technical Efficacy Thesaurus, Application Domain, Technology Topic, Popular Technical Reports.
© 2025 PatSnap. All rights reserved.Legal|Privacy policy|Modern Slavery Act Transparency Statement|Sitemap|About US| Contact US: help@patsnap.com