Tenon connection structure design method for turbine rotor of long-service-life small turbofan engine
A technology of turbofan engine and connecting structure, applied in geometric CAD and other directions, can solve the problems of uneven stress distribution on the side and back of the blade basin, high risk of engine damage, low cycle fatigue damage, etc., to reduce the stress level and improve the bearing capacity. capacity, the effect of improving the bearing capacity of the structure
- Summary
- Abstract
- Description
- Claims
- Application Information
AI Technical Summary
Problems solved by technology
Method used
Image
Examples
Embodiment Construction
[0024] In order to make the purpose, content, and advantages of the present invention clearer, the specific implementation manners of the present invention will be further described in detail below in conjunction with the accompanying drawings and embodiments.
[0025] A method for designing a tenon connection structure for a long-life small turbofan engine turbine rotor according to the present invention, the method includes the following steps:
[0026] The first step is to design the tenon connection structure as a four-tooth fir tree-shaped tenon connection structure, in which the bottom of the tenon and groove is a rounded transition, and the characteristic dimensions of the tenon head include neck width, tooth height, tooth root fillet, and tenon tooth fillet , tooth pitch, wedge angle, tooth profile angle, pressure angle, tooth bottom width, tooth bottom thickness, such as Figure 4 As shown; the characteristic dimensions of the tenon and groove include tooth height, te...
PUM
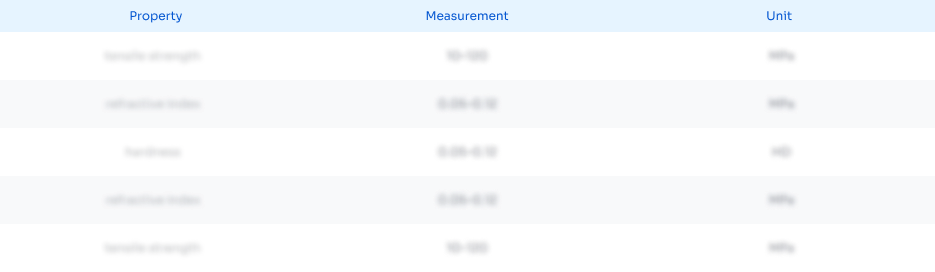
Abstract
Description
Claims
Application Information

- R&D
- Intellectual Property
- Life Sciences
- Materials
- Tech Scout
- Unparalleled Data Quality
- Higher Quality Content
- 60% Fewer Hallucinations
Browse by: Latest US Patents, China's latest patents, Technical Efficacy Thesaurus, Application Domain, Technology Topic, Popular Technical Reports.
© 2025 PatSnap. All rights reserved.Legal|Privacy policy|Modern Slavery Act Transparency Statement|Sitemap|About US| Contact US: help@patsnap.com