Enzyme staining Lyocell fiber fabric and preparation method thereof
A fabric and fiber technology, applied in the field of lyocell fiber, can solve the problems of less technology, high dyeing cost, limited source of raw materials, etc., achieve good skin-friendly performance and improve quality grade
- Summary
- Abstract
- Description
- Claims
- Application Information
AI Technical Summary
Problems solved by technology
Method used
Image
Examples
Embodiment 1
[0024] In this embodiment, an enzyme-dyed lyocell fiber fabric is prepared by the following method, including the following steps:
[0025] (1) Ammonification modification: prepare a mixed solution, immerse 100g lyocell fiber fabric into 1000mL mixed solution, immersion time is 3.5 hours, immersion temperature is 55°C, stir the reaction solution system every 30 minutes after immersion; after the reaction , washed with water, and dried; the preparation method of the mixed solution is as follows: 1000mL concentration of 10% formaldehyde solution, 100mL concentration of 4% ammonia solution and 15g of boric acid are mixed and stirred evenly.
[0026] (2) Enzyme dyeing: 100g of lyocell fabric treated in step (1) is immersed in 1000mL of aqueous solution of laccase and 2,3,4-trihydroxybenzoic acid for cultivation, laccase and 2,3,4 - The concentrations of trihydroxybenzoic acid are: 25mg / L and 150mg / L respectively; the cultivation time is 6.5 hours, and the cultivation temperature i...
Embodiment 2
[0028] In this embodiment, an enzyme-dyed lyocell fiber fabric is prepared by the following method, including the following steps:
[0029] (1) Ammonification modification: prepare a mixed solution, immerse 100g lyocell fiber fabric into 800mL mixed solution, immerse for 3 hours, immerse in a temperature of 50°C, stir the reaction solution system every 30 minutes after immersion; after the reaction , washed with water, and dried; the preparation method of the mixed solution is as follows: 1000 mL of 8% formaldehyde solution, 100 mL of 3% ammonia solution and 20 g of boric acid are mixed and stirred evenly.
[0030] (2) Enzyme dyeing: immerse 100g of lyocell fabric treated in step (1) into 800mL aqueous solution of laccase and p-diphenol for cultivation, the concentrations of laccase and p-diphenol are respectively: 20mg / L, 100mg / L; the cultivation time is 5 hours, and the cultivation temperature is 20°C; after the cultivation, the lyocell fiber fabric is washed with clear wate...
Embodiment 3
[0032] In this embodiment, an enzyme-dyed lyocell fiber fabric is prepared by the following method, including the following steps:
[0033] (1) Ammonification modification: prepare a mixed solution, immerse 100g lyocell fiber fabric into 1200mL mixed solution, immerse for 4 hours, immerse in a temperature of 60°C, stir the reaction solution system every 30 minutes after immersion; after the reaction , washed with water, and dried; the preparation method of the mixed solution is as follows: 1500 mL of 10% formaldehyde solution, 150 mL of 4% ammonia solution and 20 g of boric acid are mixed and stirred evenly.
[0034] (2) Enzyme dyeing: 100g of lyocell fiber fabric treated in step (1) was immersed in 1200mL aqueous solution of laccase and 3-amino-4-hydroxybenzenesulfonic acid for cultivation, laccase and 3-amino-4 The concentrations of -hydroxybenzenesulfonic acid are: 30mg / L and 200mg / L respectively; the cultivation time is 8 hours, and the cultivation temperature is 25°C; aft...
PUM
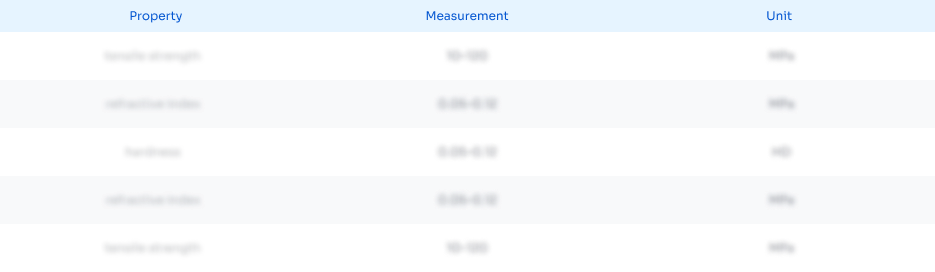
Abstract
Description
Claims
Application Information

- R&D
- Intellectual Property
- Life Sciences
- Materials
- Tech Scout
- Unparalleled Data Quality
- Higher Quality Content
- 60% Fewer Hallucinations
Browse by: Latest US Patents, China's latest patents, Technical Efficacy Thesaurus, Application Domain, Technology Topic, Popular Technical Reports.
© 2025 PatSnap. All rights reserved.Legal|Privacy policy|Modern Slavery Act Transparency Statement|Sitemap|About US| Contact US: help@patsnap.com