A distributed strain micro-crack detection system and method based on stacked autoencoders
A stacked autoencoder and distributed strain technology, applied in the field of pattern recognition, can solve problems such as unmeasured and easy to miss cracks, and achieve improved detection results, high robustness, and remarkable results
- Summary
- Abstract
- Description
- Claims
- Application Information
AI Technical Summary
Problems solved by technology
Method used
Image
Examples
Embodiment Construction
[0051] Below in conjunction with accompanying drawing, the present invention is described in further detail:
[0052] see Figure 1 to Figure 5 , a distributed strain crack detection system based on stacked autoencoders, including a strain sequence acquisition module; a strain sequence preprocessing module; a feature self-learning and characterization module based on stacked autoencoders; a Softmax classification recognition module (the specific process is as follows figure 1 shown).
[0053] The strain sequence collection module is used to collect the distributed strain of the structure, and the collected distributed strain of the structure is a one-dimensional sequence;
[0054] The strain sequence preprocessing module includes: a z-score normalization module and a sliding window module, and the z-score normalization module normalizes the strain sequence to data with 0 mean and 1 standard deviation. The sliding window module intercepts a set of strain subsequences of lengt...
PUM
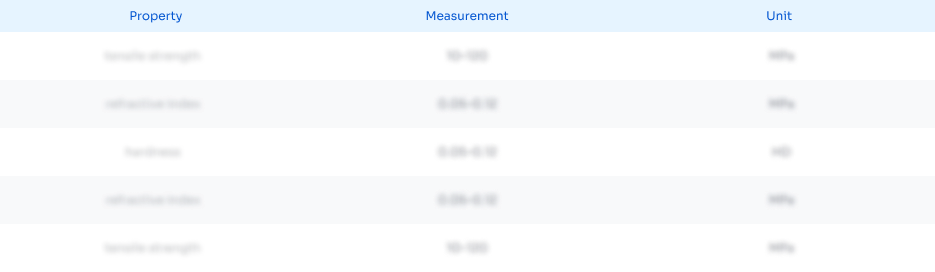
Abstract
Description
Claims
Application Information

- Generate Ideas
- Intellectual Property
- Life Sciences
- Materials
- Tech Scout
- Unparalleled Data Quality
- Higher Quality Content
- 60% Fewer Hallucinations
Browse by: Latest US Patents, China's latest patents, Technical Efficacy Thesaurus, Application Domain, Technology Topic, Popular Technical Reports.
© 2025 PatSnap. All rights reserved.Legal|Privacy policy|Modern Slavery Act Transparency Statement|Sitemap|About US| Contact US: help@patsnap.com