Forming method of straight-wall cylindrical piece with uniform wall thickness
A cylindrical part and straight wall technology, applied in the field of forming straight wall cylindrical parts, can solve the problems of low cost, short processing cycle and long cycle, and achieve the effects of low cost, uniform wall thickness and short forming cycle
- Summary
- Abstract
- Description
- Claims
- Application Information
AI Technical Summary
Problems solved by technology
Method used
Image
Examples
Embodiment Construction
[0038] The schematic diagram of the geometric parameters of the target straight wall cylindrical part is as follows figure 1 As shown, D=78mm, H=39mm, r=12mm, t=0.3mm, according to the principle of constant volume, t 0 =t / [D 2 / (D 2 -2(4-π)Dr)+4(3-π)r 2 +4DH]=0.84mm, choose 1060 aluminum with a thickness of 0.84mm as the original sheet, the forming limit angle is 67°, and the axial feed is 0.4mm.
[0039] The first pass adopts a three-stage forming path, and the radius is R=D / 2=39mm, and the depth is H from top to bottom. 1 =0.515D+0.0001667(D-58)(D-78)-5.291e-7(D-118)(D-58)(D-78)+0.83=41mm three-step cone barrel: the first straight line The forming angle is θ 1 =64°, the distance between the starting point of the straight line and the central axis is R=39mm, the distance between the end of the first segment of the straight line and the central axis is L 2=0.365D+0.0002083(D-58)(D-78)-1.918e-6(D-118)(D-58)(D-78)-0.37=29.4mm; the forming angle of the second straight line ...
PUM
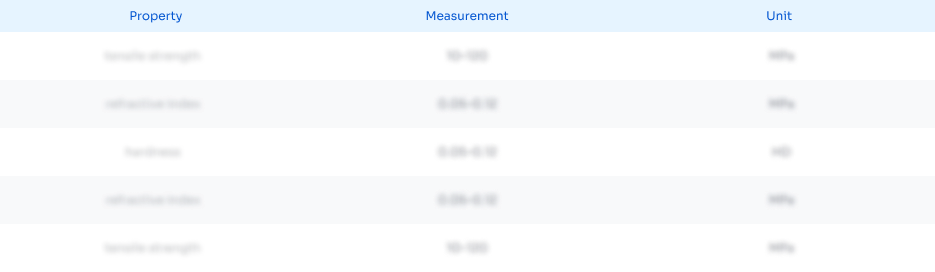
Abstract
Description
Claims
Application Information

- Generate Ideas
- Intellectual Property
- Life Sciences
- Materials
- Tech Scout
- Unparalleled Data Quality
- Higher Quality Content
- 60% Fewer Hallucinations
Browse by: Latest US Patents, China's latest patents, Technical Efficacy Thesaurus, Application Domain, Technology Topic, Popular Technical Reports.
© 2025 PatSnap. All rights reserved.Legal|Privacy policy|Modern Slavery Act Transparency Statement|Sitemap|About US| Contact US: help@patsnap.com