Butyl rubber sheet cutting machine
A butyl rubber and cutting machine technology, applied in metal processing and other directions, can solve problems such as waste and inconvenience in use, and achieve the effects of convenient use, improved production efficiency and simple structure
- Summary
- Abstract
- Description
- Claims
- Application Information
AI Technical Summary
Problems solved by technology
Method used
Image
Examples
Embodiment 1
[0034] Such as figure 1In the shown first embodiment of the butyl rubber sheet cutting machine of the present invention, the butyl rubber sheet cutting machine includes a workbench 100 on which a feeding platform 200, a cutting mechanism 300 and an inverted The material mechanism 400, the cutting mechanism 300 includes a fixed knife bracket 310 and a moving knife bracket 320, the fixed knife bracket 310 includes a horizontal base 311 and a support arm 312 connected in an L-shaped structure, and one end of the moving knife bracket 320 is connected to the horizontal base 311 The hinged part 313 of the end is hinged, and the top of the support arm 312 is connected with an operating rod 330, and the operating rod 330 is connected with the other end of the movable knife bracket 320; There is a movable blade 321 on the top, and the rear side of the fixed blade 314 is staggered with the movable blade 321; the feeding platform 200 is connected to the front side of the fixed blade 314,...
Embodiment 2
[0047] The connection relationship and working principle of each component in this embodiment are the same as those in Embodiment 1, the difference is that, as Figure 5 As shown, the top of the support arm 312 in this embodiment is provided with a large fan-shaped tooth 360, and one end of the operating lever 330 is provided with a small fan-shaped tooth 370, and the large fan-shaped tooth 360 meshes with the small fan-shaped tooth 370; A central shaft is arranged and fixed, and the end of the movable knife bracket 320 away from the hinge portion 313 is movably connected with the central shaft. The large fan-shaped teeth 360 and the small fan-shaped teeth 370 are meshed for transmission, which can rotate flexibly, and can make the operating rod 330 produce the effect of decelerating and increasing force on the moving knife bracket 320, thereby enhancing the cutting ability of the cutting mechanism 300 and improving the service life.
PUM
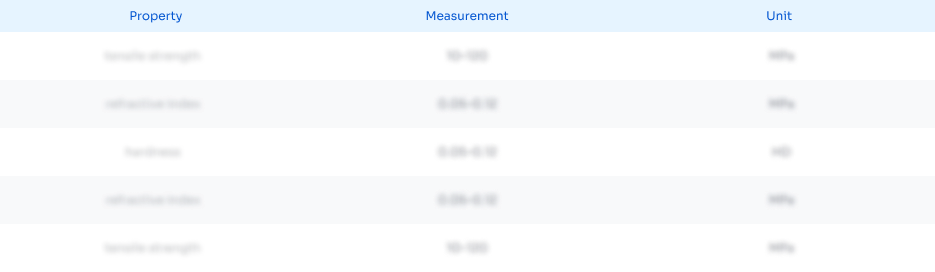
Abstract
Description
Claims
Application Information

- Generate Ideas
- Intellectual Property
- Life Sciences
- Materials
- Tech Scout
- Unparalleled Data Quality
- Higher Quality Content
- 60% Fewer Hallucinations
Browse by: Latest US Patents, China's latest patents, Technical Efficacy Thesaurus, Application Domain, Technology Topic, Popular Technical Reports.
© 2025 PatSnap. All rights reserved.Legal|Privacy policy|Modern Slavery Act Transparency Statement|Sitemap|About US| Contact US: help@patsnap.com