Splicing construction method of corrugated steel pipe gallery
A technology of corrugated steel pipes and construction methods, applied in artificial islands, water conservancy projects, infrastructure projects, etc., can solve problems such as heavy maintenance workload, high labor costs, and lack of splicing methods
- Summary
- Abstract
- Description
- Claims
- Application Information
AI Technical Summary
Problems solved by technology
Method used
Image
Examples
Embodiment Construction
[0098] Such as Figure 12 A splicing construction method of a corrugated steel pipe gallery is shown, and the constructed pipe gallery is a corrugated steel pipe gallery; combined with figure 1 , figure 2 , image 3 , Figure 4 , Figure 5 , Figure 7 , Figure 8 and Figure 9 , the corrugated steel pipe gallery includes a pipe gallery body spliced by a plurality of pipe gallery splicing sections 1 and a prestressed reinforcement structure arranged outside the pipe gallery body, the pipe gallery body is arranged horizontally, and multiple pipe gallery The splicing sections 1 are arranged on the same straight line from back to front along the longitudinal extension direction of the constructed pipe gallery; The pipe diameters of the splicing section 1 of the pipe gallery are the same, each of the corrugated steel pipes is a straight steel pipe, and the cross-sectional structure and size of all the corrugated steel pipes in the pipe gallery body are the same; multiple ...
PUM
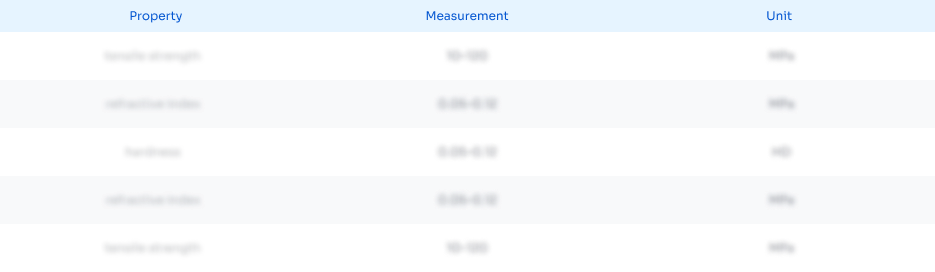
Abstract
Description
Claims
Application Information

- R&D
- Intellectual Property
- Life Sciences
- Materials
- Tech Scout
- Unparalleled Data Quality
- Higher Quality Content
- 60% Fewer Hallucinations
Browse by: Latest US Patents, China's latest patents, Technical Efficacy Thesaurus, Application Domain, Technology Topic, Popular Technical Reports.
© 2025 PatSnap. All rights reserved.Legal|Privacy policy|Modern Slavery Act Transparency Statement|Sitemap|About US| Contact US: help@patsnap.com