Ultrafine equipment oscillation mechanism
A technology of oscillating mechanism and equipment, applied in the directions of ultra-finishing machines, metal processing equipment, manufacturing tools, etc., can solve problems such as limitations, and achieve the effects of stable amplitude and vibration frequency, ensuring coaxiality, and adjustable amplitude and vibration frequency.
- Summary
- Abstract
- Description
- Claims
- Application Information
AI Technical Summary
Problems solved by technology
Method used
Image
Examples
Embodiment 1
[0045] like Figures 1 to 6 As shown, an oscillation mechanism for ultra-precision equipment includes a vertically arranged rotary drive device 1 and an oscillator seat 2 coaxially sleeved outside the rotary shaft 11 of the rotary drive device 1, and also includes:
[0046] An amplitude adjustment assembly 3, the amplitude adjustment assembly 3 is installed below the rotating shaft 11, and it rotates synchronously with the rotating shaft 11; and
[0047]The oscillator longitudinal pin 4, the oscillator longitudinal pin 4 is coaxially installed inside the oscillator seat 2, and is located below the amplitude adjustment assembly 3, the oscillator longitudinal pin 4 includes The working end 41 and the matching end 42 of the end, the working end 41 is always in conflict with the object to be oscillated, and the matching end 42 is protruded along its circumferential direction to intermittently interfere with the amplitude adjustment assembly 3 raised portion a421;
[0048] The ro...
Embodiment 2
[0055] Figure 7 It is a schematic structural view of Embodiment 2 of an ultra-precision equipment oscillation mechanism of the present invention; as Figure 7 As shown, the components that are the same as or corresponding to those in Embodiment 1 use the corresponding reference numerals as in Embodiment 1. For the sake of simplicity, only the differences from Embodiment 1 will be described below. The Example 2 with figure 1 Example 1 shown differs in that:
[0056] like Figure 7 As shown, an oscillation mechanism of ultra-precision equipment, the control part 31 is a ball installed on the lower end of the rotating shaft 11 .
[0057] It should be noted that, different from Embodiment 1, the control part 31 in this embodiment is a ball structure, which directly rolls and is placed in the groove at the lower end of the rotating shaft 11 .
[0058] It should be noted that, compared with the control part 31 provided with bumps, the control part 31 with the ball structure has...
Embodiment 3
[0060] Figure 8 It is a structural schematic diagram of Embodiment 3 of an ultra-precision equipment oscillation mechanism of the present invention; as Figure 8 As shown, the components that are the same as or corresponding to those in Embodiment 2 use the corresponding reference numerals as in Embodiment 2. For the sake of simplicity, only the differences from Embodiment 2 will be described below.
[0061] like Figure 8 and Figure 9 As shown, an oscillating mechanism for ultra-precision equipment also includes an elastic connector 5 coaxially sleeved outside the rotating shaft 11, and sequentially includes transition connections along its axial direction from top to bottom. The claw part 51 and the threaded part 52, the claw part 51 includes a plurality of claws 511 equidistantly arranged along the axial circumference, and there is an adjustment gap 512 between two adjacent claws 511, and the The diameter of the end portion of the claw portion 51 away from the threaded...
PUM
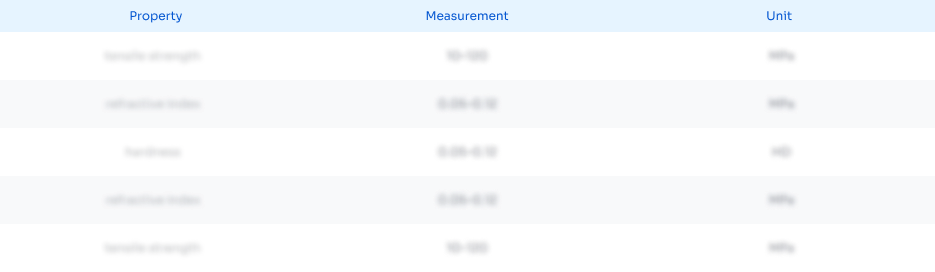
Abstract
Description
Claims
Application Information

- R&D
- Intellectual Property
- Life Sciences
- Materials
- Tech Scout
- Unparalleled Data Quality
- Higher Quality Content
- 60% Fewer Hallucinations
Browse by: Latest US Patents, China's latest patents, Technical Efficacy Thesaurus, Application Domain, Technology Topic, Popular Technical Reports.
© 2025 PatSnap. All rights reserved.Legal|Privacy policy|Modern Slavery Act Transparency Statement|Sitemap|About US| Contact US: help@patsnap.com