Method for improving cold strength of coke
A cold-strength, high-strength technology, applied in the coking oven, petroleum industry, etc., can solve the problems of high coal quality index requirements for fat coal, poor practicability, complicated methods, etc., achieve good environmental and economic benefits, and reduce the use of efficiency and reduce production costs
- Summary
- Abstract
- Description
- Claims
- Application Information
AI Technical Summary
Problems solved by technology
Method used
Image
Examples
Embodiment 1
[0027] The gas coal with a particle size of less than 6mm from the production plant is added to the crusher for crushing. After crushing, the particle size of the gas coal is screened and analyzed. After crushing, the proportion of the particle size of the gas coal smaller than 3mm is 48%. The processed gas coal is blended with other types of coal. The proportion of gas coal in the entire blended coal is 25.5%, and the ash content of the blended coal after blending is A d =8%, the volatile matter is VM d = 28%. Add the blended coal into the crusher for repeated crushing. The groove spacing of the crusher is 3mm, and the proportion of the crushed blended coal with particle size less than 3mm is 86%. Use a spraying device to mix a certain amount of water into the crushed blended coal to facilitate even moisture blending and ensure that the moisture content of the blended coal is 4%. Finally, add the blended coal to 40kg of coke oven and heat it at a heating rate of 4°C / min. 10...
Embodiment 2
[0030] The gas coal with a particle size of less than 6mm from the production plant is added to the crusher for crushing. After crushing, the particle size of the gas coal is screened and analyzed. After crushing, the proportion of the particle size of the gas coal smaller than 3mm is 50%. The processed gas coal is blended with other types of coal. The proportion of gas coal in the entire blended coal is 26%, and the ash content of the blended coal after blending is A d =9%, the volatile matter is VM d = 27%. Add the blended coal into the crusher for repeated crushing. The groove spacing of the crusher is 3.5mm, and the proportion of the crushed blended coal with a particle size less than 3mm is 85%. Use a spraying device to mix a certain amount of water into the crushed blended coal to facilitate even moisture blending and ensure that the moisture content of the blended coal is 5%. Finally, add the blended coal to a 40kg coke oven and heat it at a heating rate of 4°C / min. 1...
Embodiment 3
[0033] The gas coal with a particle size of less than 6mm from the production plant is added to the crusher for crushing. After crushing, the particle size of the gas coal is screened and analyzed. After crushing, the proportion of the particle size of the gas coal smaller than 3mm is 51%. The processed gas coal is blended with other types of coal. The proportion of gas coal in the entire blended coal is 26.5%, and the ash content of the blended coal after blending is A d =9.5%, the volatile matter is VM d = 26.5%. Add the blended coal into the crusher for repeated crushing. The groove spacing of the crusher is 4mm, and the proportion of the crushed blended coal with particle size less than 3mm is 84%. Use a spraying device to mix a certain amount of water into the crushed blended coal to facilitate even moisture blending and ensure that the moisture content of the blended coal is 6%. Finally, add the blended coal to a 40kg coke oven and heat it at a heating rate of 4°C / min. ...
PUM
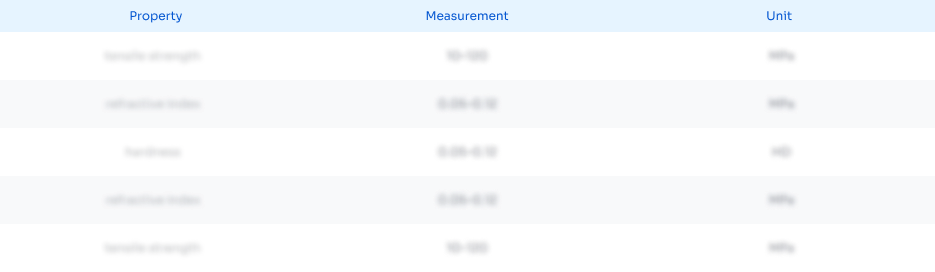
Abstract
Description
Claims
Application Information

- R&D
- Intellectual Property
- Life Sciences
- Materials
- Tech Scout
- Unparalleled Data Quality
- Higher Quality Content
- 60% Fewer Hallucinations
Browse by: Latest US Patents, China's latest patents, Technical Efficacy Thesaurus, Application Domain, Technology Topic, Popular Technical Reports.
© 2025 PatSnap. All rights reserved.Legal|Privacy policy|Modern Slavery Act Transparency Statement|Sitemap|About US| Contact US: help@patsnap.com