Loading device of wing hanging connector
A technology for hanging joints and loading devices, which is applied in the direction of measuring devices, testing of mechanical components, testing of machine/structural components, etc., and can solve the problem of the launch of loading devices for hanging joints, the short distance, and the inability to apply loads by actuators, etc. problems, to achieve the effect of reducing test cost and risk, convenient disassembly and assembly, and simple structure
- Summary
- Abstract
- Description
- Claims
- Application Information
AI Technical Summary
Problems solved by technology
Method used
Image
Examples
Embodiment
[0062] Refer below Figure 1 to Figure 4 The loading device of the wing suspension joint of a specific embodiment of the present invention is described.
[0063] Such as figure 1 As shown, the loading device of the wing suspension joint is used to ensure that the engine load is accurately transmitted to the suspension joint of the wing. The suspension joint includes an upper joint 11, an inner lower joint 12, an outer lower joint 13, and a lateral joint 14. The rear joint 15, the loading device includes a T-shaped hanging dummy 2, a first heading joint 31, a second heading joint 32, a third heading joint 33, a matching lateral joint 4, a first vertical joint 51 and a second Vertical joint 52, the hanging dummy 2 is connected with the hanging joint, the T-shaped hanging dummy 2 includes the first wall plate 21 and the second wall plate 22, the first wall plate 21 is connected with the hanging joint, the second wall The board 22 is connected to the end of the first wall board ...
PUM
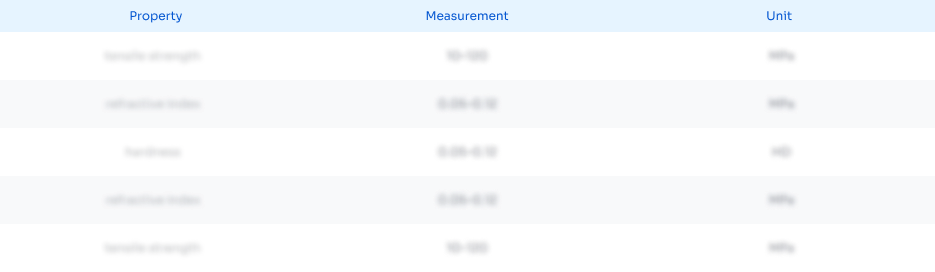
Abstract
Description
Claims
Application Information

- Generate Ideas
- Intellectual Property
- Life Sciences
- Materials
- Tech Scout
- Unparalleled Data Quality
- Higher Quality Content
- 60% Fewer Hallucinations
Browse by: Latest US Patents, China's latest patents, Technical Efficacy Thesaurus, Application Domain, Technology Topic, Popular Technical Reports.
© 2025 PatSnap. All rights reserved.Legal|Privacy policy|Modern Slavery Act Transparency Statement|Sitemap|About US| Contact US: help@patsnap.com